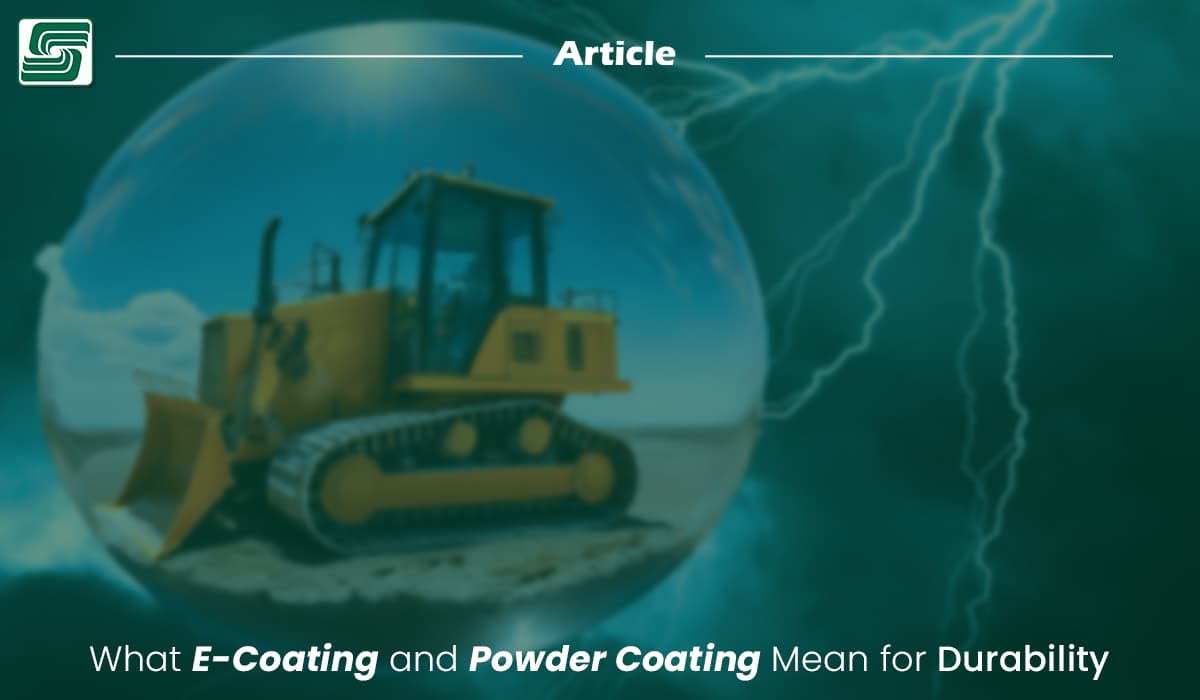
Protective metal coatings have a rich history of innovation. In 1950, the introduction of Carbozinc 11 transformed steel fabrication with its self-curing, inorganic zinc primer.
By the 1960s, industries began replacing lead-based paints with advanced coatings like Carbozinc 11, especially on steel bridges.
The automotive sector was among the first to recognize the importance of these coatings, using methods like e-coating to protect intricate parts from corrosion. Over time, advancements such as secondary containment linings in the 1990s further enhanced environmental safety, showcasing the evolving role of coatings in durability and sustainability.
How E-Coating Enhances Durability
What Is E-Coating?
E-coating, also known as electrocoating or electrodeposition, is an advanced industrial coating process that applies a protective layer to metal surfaces. This method uses an electric charge to bond paint particles to conductive materials, creating a uniform and durable finish.
Unlike traditional painting methods, e-coating ensures complete coverage, even on complex shapes and hard-to-reach areas. Its ability to provide superior corrosion resistance makes it a preferred choice for industries requiring high corrosion protection, such as automotive and aerospace.
E-coating combines electrochemistry and material science to enhance performance and durability. Immersing metal parts in a water-based solution ensures consistent coating thickness across the entire surface. This uniformity improves wear resistance and reduces the risk of rust and degradation.
The E-Coating Process Explained
The e-coating process involves several precise steps to ensure optimal results.
- Surface Preparation: Metal parts undergo cleaning and pretreatment to remove contaminants like grease, dirt, and rust. This step ensures proper coating adhesion.
- Immersion in the E-Coating Bath: The parts are submerged in a water-based solution containing paint particles. An electrical current is applied, causing the particles to migrate and adhere to the metal surface.
- Controlled Coating Thickness: The electrical charge allows precise coating thickness control, typically ranging from 15 to 35 microns—ensuring effective corrosion protection without overcoating.
- Curing: The coated parts are baked in an oven to cure the finish. This step solidifies the protective layer, enhancing its durability and resistance to environmental factors.
This process provides superior corrosion resistance and minimizes waste, making it an environmentally friendly option. Its ability to control thickness ensures consistent quality, even for intricate designs.
Durability Benefits of E-Coating
E-coating increases durability significantly. By creating a robust barrier against environmental damage. Its key properties contribute to its effectiveness:
Property |
Contribution to Durability |
Increased Durability |
Thickness enhances durability, creating a robust barrier for long-lasting protection. |
Better Protection |
Superior coverage shields substrates from external aggressors, enhancing overall protection. |
Corrosion Resistance |
Proven superior resistance against environmental elements, ensuring long-lasting durability. |
Controlled Film Thickness |
Precise control of thickness (15 to 35 microns) ensures effective corrosion protection. |
The protective layer formed during the e-coating process offers corrosion and UV protection, making it ideal for harsh environments. Its ability to provide high corrosion protection reduces maintenance costs and extends the lifespan of coated materials.
E-coating remains a top choice for industries seeking reliable and sustainable solutions when combining superior corrosion resistance with environmental friendliness.
Common Applications of E-Coating
E-coating has become a versatile solution for industries that demand durable and reliable finishes.
Its ability to provide uniform coverage and superior corrosion resistance makes it suitable for several applications. Below are some of the most common uses of e-coating across various sectors:
Automotive Industry
The automotive sector relies heavily on e-coating to protect vehicle components from rust and wear. Manufacturers use this process to coat parts, such as:
- Chassis and frames
- Suspension systems
- Engine components
- Brake calipers
E-coating ensures these parts remain resistant to harsh conditions, including moisture, road salt, and extreme temperatures. Its ability to coat intricate shapes makes it ideal for small, complex automotive parts.
Aerospace Industry
In aerospace, e-coating plays a critical role in enhancing the durability of aircraft components.
It protects metal parts from corrosion caused by high altitudes and varying weather. Commonly coated items include:
- Landing gear assemblies
- Cabin interiors
- Structural components
The lightweight and uniform finish e-coating provides aligns with the aerospace industry's need for precision and efficiency.
Consumer Electronics
E-coating is widely used in the production of consumer electronics.
It provides a protective layer for metal casings, ensuring resistance to scratches and environmental damage. Examples include:
- Smartphone frames
- Laptop casings
- Wearable device components
This application improves durability and enhances the aesthetic appeal of electronic devices.
Industrial Equipment
Heavy machinery and industrial tools benefit from e-coating because they withstand tough environments. Common applications include:
- Agricultural equipment
- Construction machinery
- Metal storage tanks
E-coating protects these items from corrosion, extending their lifespan and reducing maintenance costs.
Medical Devices
The medical field uses e-coating to ensure the longevity and safety of metal instruments. It provides a smooth, non-porous surface that resists corrosion and facilitates sterilization. Examples include:
- Surgical tools
- Hospital beds
- Wheelchair frames
This application highlights the versatility of e-coating in meeting strict hygiene and durability standards.
NOTE: E-coating is especially effective for parts with complex geometries or hard-to-reach areas, making it a preferred choice for intricate designs.
Industry |
Commonly Coated Items |
Automotive |
Chassis, suspension systems, engine components, brake calipers |
Aerospace |
Landing gear, cabin interiors, structural components |
Consumer Electronics |
Smartphone frames, laptop casings, wearable device components |
Industrial Equipment |
Agricultural machinery, construction tools, metal storage tanks |
Medical Devices |
Surgical tools, hospital beds, wheelchair frames |
E-coating's adaptability across these industries shows its importance in enhancing the durability and performance of metal products.
Its ability to provide consistent protection ensures long-lasting results, even in demanding environments.
How Powder Coating Enhances Durability
What Is Powder Coating?
Powder coating is a dry finishing process that applies a protective and decorative layer to metal surfaces. Unlike traditional liquid paints, it uses fine powder from polymer resins, pigments, and other additives.
This powder adheres to the surface through electrostatic energy before being cured under heat. The result is a smooth, durable finish that resists wear and tear.
This method is widely recognized for its ability to create a thicker and more uniform coating compared to liquid paints.
It eliminates the risk of drips or uneven application, ensuring a consistent appearance.
Powder coating is also environmentally friendly, producing minimal waste and containing no volatile organic compounds (VOCs).
The Powder Coating Process Explained
The powder coating process involves several key steps to achieve a durable and high-quality finish:
- Surface Preparation: The metal surface is cleaned and pretreated to remove dirt, grease, and rust. This step ensures the powder's proper adhesion.
- Application of Powder: A specialized spray gun applies the powder to the surface. Electrostatic energy charges the powder particles, causing them to stick to the metal.
- Curing: The coated item is placed in an oven, where heat melts the powder and bonds it to the surface. This step creates a hard, protective layer.
The powder coating process is efficient and versatile, making it suitable for various materials and applications. Its consistent coverage ensures long-lasting results, even for complex shapes.
Durability Benefits of Powder Coating
Powder coating offers exceptional durability, making it a preferred choice for industries that demand long-lasting finishes. Its key advantages include:
- Resistance to Damage: Powder coating resists scratching, peeling, and chipping better than traditional paint. The electrostatic bond allows the coating to move with the metal, reducing the risk of flaking.
- Corrosion Protection: The thick, uniform layer blocks corrosive agents like moisture and chemicals from reaching the metal surface, enhancing the lifespan of coated items.
- UV and Chemical Resistance: Certain formulations provide additional protection against UV light and harsh chemicals, making them ideal for outdoor and industrial applications.
- Eco-Friendly Durability: Powder coating produces minimal waste and contains no harmful VOCs, aligning durability with environmental sustainability.
Material |
Powder Coating Benefits |
Steel Alloys |
Provides extra protection against corrosion and wear. |
Aluminum |
Lightweight, sturdy, and readily accepted powder coating. |
Chrome |
It can be coated but requires extra work to maintain shine. |
Copper, Brass, Bronze |
It is effective for decorative purposes but not for heavy-duty parts. |
Powder coating stands out for its superior durability while maintaining aesthetic appeal. Its thicker coating and resistance to environmental factors make it a reliable choice for automotive and construction industries.
Powder coating offers protection and longevity, ensuring that metal surfaces remain functional and visually appealing for years.
Common Applications of Powder Coating
Powder coating has become a go-to solution for industries that demand durable and visually appealing finishes.
Its versatility protects and enhances various products, from heavy machinery to everyday consumer goods.
Below are some of the most common powder-coating applications across various sectors.
Automotive Industry
The automotive sector relies heavily on powder coating to protect components from wear and corrosion. This process is used to coat parts such as:
- Wheels and rims
- Bumpers and grilles
- Suspension components
- Engine parts
Powder coating provides a tough, chip-resistant finish that withstands road debris, extreme temperatures, and moisture. Its ability to create vibrant colors also enhances vehicles' aesthetic appeal.
Construction and Architecture
In construction, powder coating ensures the longevity of metal structures exposed to harsh weather. Architects and builders use it to coat:
- Window frames
- Railings and fences
- Light poles
- Roofing panels
The protective layer resists rust, fading, and scratches, making it ideal for outdoor applications. Its eco-friendly nature aligns with the growing demand for sustainable building materials.
Consumer Goods
Powder coating enhances the durability and appearance of everyday items. Manufacturers apply it to products like:
- Appliances (refrigerators, washing machines)
- Furniture (metal chairs, tables)
- Sports equipment (bicycles, gym machines)
This coating protects against wear and tear and offers a smooth, attractive finish that appeals to consumers.
Industrial Equipment
Heavy-duty machinery benefits from the robust protection offered by powder coating. Commonly coated items include:
- Agricultural tools
- Construction Equipment
- Storage racks and shelves
The thick, uniform layer shields these items from chemicals, moisture, and physical damage, extending their operational life.
Electronics and Electrical Components
Powder coating is widely used in the electronics industry to protect sensitive components. Examples include:
- Electrical enclosures
- Circuit boards
- Metal casings for devices
This application ensures resistance to heat, moisture, and electrical interference, making it essential for reliable performance.
Industry |
Commonly Coated Items |
Automotive |
Wheels, bumpers, suspension parts, engine components |
Construction |
Window frames, railings, light poles, roofing panels |
Consumer Goods |
Appliances, furniture, sports equipment |
Industrial Equipment |
Agricultural tools, construction machinery, storage racks |
Electronics |
Electrical enclosures, circuit boards, device casings |
NOTE: Powder coating is effective for outdoor and high-traffic applications because of its resistance to UV rays, chemicals, and physical damage.
Powder coating’s adaptability across these industries highlights its importance in creating durable, long-lasting products. Its ability to combine protection with aesthetic appeal ensures it remains a preferred choice for manufacturers worldwide.
E-Coating vs. Powder Coating: Key Durability Differences
Comparing Application Methods
E-coating and powder coating differ significantly in their application methods, each tailored to specific needs. E-coating involves immersing the metal part in a bath containing a water-based paint or epoxy solution.
An electric current attracts the paint particles to the surface, ensuring a uniform and controlled coating thickness.
This method excels in coating intricate shapes and hard-to-reach areas, making it ideal for automotive and marine applications.
In contrast, powder coating uses a dry powder applied electrostatically to the metal surface. The coated part is then cured under heat, creating a thicker and more durable finish.
This process is better suited for outdoor furniture, appliances, and heavy-duty equipment requiring robust protection.
Feature |
E-Coating |
Powder Coating |
Application Method |
Immersion in a liquid bath with electric current |
Electrostatic application of dry powder |
Coating Thickness |
Thin and uniform |
Thicker and more robust |
Ideal Use |
Intricate shapes, corrosion protection |
Outdoor and high-impact applications |
E-coating provides precision and consistency, while powder coating offers durability and visual appeal. Both methods cater to different industrial needs, ensuring optimal performance for specific applications.
Durability in Harsh Environments
Both e-coating and powder coating enhance durability, but their performance varies in challenging conditions. E-coating offers exceptional corrosion resistance, making it suitable for parts exposed to harsh chemicals or underwater environments.
Its ability to coat complex shapes ensures complete protection, even in the most demanding scenarios.
Powder coating excels in impact resistance and UV protection. Its thick, durable layer shields metal surfaces from physical stress, moisture, and sunlight, making it a preferred choice for outdoor applications such as construction materials and automotive exteriors.
- E-coating:
- Exceptional corrosion resistance.
- Uniform coverage for intricate designs.
- It is ideal for underwater or chemical exposure.
- Powder coating:
- Superior impact resistance.
- Protection against UV rays and weathering.
- Best for outdoor and high-traffic environments.
Each method shows unique strengths, ensuring durability in specific environmental conditions.
E-Coating Strengths
E-coating stands out for its versatility and precision. Its ability to provide complete coverage ensures long-term durability, even for complex shapes, making it a reliable choice for industries like automotive, aerospace, and medical equipment.
- Excels in corrosion resistance, protecting metal surfaces from rust and degradation
- Offers durability and cost-effectiveness over time, reducing maintenance needs
- It provides uniform coating thickness, enhancing longevity and performance
- Adapts to various industries, from automotive parts to surgical tools
E-coating combines precision with durability, making it an essential solution for applications requiring high corrosion protection and intricate designs.
Powder Coating Strengths
Powder coating offers several advantages, making it a preferred choice for durable and visually appealing finishes. Its unique properties ensure long-lasting protection and aesthetic value across various applications.
- Enhanced Durability: Powder coating creates a thick, uniform layer that resists scratches, chipping, and peeling. This durability ensures that coated surfaces withstand physical stress and environmental exposure.
- Corrosion Resistance: The protective layer blocks moisture and chemicals from reaching the metal surface, making powder coating ideal for outdoor and industrial environments.
- UV Protection: Certain powder formulations include UV-resistant properties. These coatings prevent fading and degradation caused by prolonged sun exposure, making them suitable for outdoor furniture and automotive exteriors.
- Eco-Friendly Process: Powder coating produces minimal waste and contains no volatile organic compounds (VOCs). This environmentally friendly approach aligns with modern sustainability goals.
- Aesthetic Versatility: Powder coating offers various colors, textures, and finishes, from matte to glossy. It enhances products' visual appeal while maintaining durability.
NOTE: Powder coating works well for high-traffic areas or outdoor applications where surfaces face constant wear and tear.
Feature |
Benefit |
Thick Coating |
Provides superior resistance to physical damage. |
UV Resistance |
Protects against fading and sun damage. |
Eco-Friendly |
Reduces environmental impact with minimal waste and no harmful emissions. |
Aesthetic Options |
Offers a variety of finishes for decorative and functional purposes. |
Powder coating combines strength and style, making it a versatile solution for the construction, automotive, and consumer goods industries.
When to Use E-Coating vs. Powder Coating
Choosing between e-coating and powder coating depends on the project's specific requirements.
Each method excels in different areas and offers unique benefits for durability and performance.
- E-Coating:
- Best for intricate designs or hard-to-reach areas
- Ideal for applications requiring thin, uniform coatings
- Provides superior corrosion resistance, especially in underwater or chemical environments
- Powder Coating:
- Suitable for outdoor and high-impact applications
- It offers a thicker, more robust finish for enhanced durability
- Excels in UV protection and aesthetic versatility
Factor |
E-Coating |
Powder Coating |
Application Complexity |
Excels in coating complex shapes |
Better for simpler, larger surfaces |
Corrosion Resistance |
Superior for chemical and underwater exposure |
Effective for general outdoor use |
Finish Thickness |
Thin and precise |
Thick and durable |
Aesthetic Appeal |
Limited options |
Wide range of colors and textures |
NOTE: For projects requiring both corrosion resistance and aesthetic appeal, combining e-coating with powder coating may provide optimal results.
Understanding the differences between e-coating and powder coating helps manufacturers select the right method.
They ensure long-lasting protection and performance by evaluating material type, environmental conditions, and desired finish.
Choosing the Right Coating for Your Needs
Factors to Consider: Material Type
The type of material plays a critical role in determining whether e-coat or powder coating is the better choice.
Each method offers unique advantages based on the material's properties and intended use.
- Environmental Exposure: E-coat provides superior corrosion resistance, making it ideal for materials exposed to harsh environments, such as underwater or chemical-heavy settings. Powder coating, however, excels in UV resistance and physical durability, making it suitable for outdoor applications.
- Complexity and Size of the Part: E-coat is highly effective for intricate shapes and small components because it coats hard-to-reach areas uniformly. Powder coating works better for larger, simpler parts that require a thicker, more robust finish.
- Aesthetic Preferences: Powder coating offers various colors and finishes, including matte, glossy, and textured options, making it a preferred choice for industries prioritizing visual appeal. On the other hand, e-coat provides a sleek, uniform finish that highlights design intricacies.
Understanding the material's characteristics ensures the chosen coating method aligns with functional and aesthetic requirements.
Environmental Conditions and Durability
Environmental factors significantly influence the choice between e-coat and powder coating. Each method offers distinct advantages depending on the conditions the material will face.
- E-coat:
- Provides uniform coverage, even for complex geometries
- It offers exceptional corrosion resistance, making it suitable for underwater or chemical-heavy environments
- Powder coating:
- It delivers a thicker, more durable finish, ideal for items exposed to physical stress
- Includes UV-resistant formulations, ensuring protection against fading and degradation in outdoor settings
For example, an e-coat is often used for automotive parts that encounter moisture and road salt. At the same time, powder coating is preferred for outdoor furniture and construction materials exposed to sunlight and weathering.
Selecting the right coating ensures the material withstands environmental challenges while maintaining its durability.
Cost and Efficiency of E-Coating and Powder Coating
Cost and efficiency are essential considerations when choosing between e-coat and powder coating. Each method offers unique benefits depending on the project's scale and requirements.
- E-coat:
- High-volume projects benefit from lower per-unit costs, making it cost-effective for mass production.
- Requires more energy for maintenance, which may increase operational costs over time.
- Powder coating:
- It is more labor-intensive but allows for material reuse, reducing waste.
- Larger parts and higher environmental costs often favor powder coating in cost analysis.
For smaller batches or projects requiring vibrant finishes, powder coating may provide better value.
However, because of its efficiency and precision, e-coat remains the preferred choice for intricate designs and high-volume production.
Evaluating the project's scale and budget ensures the selected method delivers optimal results.
Aesthetic Preferences and Finish Options
E-coating and powder coating offer distinct aesthetic and finish options, making them versatile for various industries.
Each method provides unique visual and functional benefits, catering to different design preferences and project requirements.
E-Coating: Sleek and Subtle Finishes
E-coating delivers a smooth, uniform finish that enhances the appearance of intricate designs. Its thin coating layer highlights fine details, making it ideal for parts requiring precision.
- Color Options: E-coating typically offers a limited range of colors, often in neutral tones like black, gray, or clear finishes. These options suit applications prioritizing functionality over bold aesthetics.
- Finish Types: The process produces a sleek, glossy surface. This finish enhances the professional look of components while providing corrosion resistance.
- Applications: Industries such as automotive and medical equipment favor e-coating because it coats small, detailed parts without compromising their design.
NOTE: E-coating works best for projects where subtlety and uniformity are more important than vibrant colors or textures.
Powder Coating: Vibrant and Versatile
Powder coating stands out for its wide range of colors, textures, and finishes.
This method allows manufacturers to achieve both durability and visual appeal.
- Color Variety: Powder coating offers an extensive palette, including bold, metallic, and custom colors. This flexibility makes it suitable for decorative and branding purposes.
- Finish Options: The process supports various finishes, such as matte, glossy, satin, and textured. These options enhance the visual appeal while hiding surface imperfections.
- Applications: Powder coating is popular in industries like construction, consumer goods, and automotive, where aesthetics play a significant role.
Feature |
E-Coating |
Powder Coating |
Color Range |
Limited (neutral tones) |
Extensive (bold, metallic, custom) |
Finish Types |
Sleek, glossy |
Matte, glossy, satin, textured |
Best Use |
Precision parts, subtle designs |
Decorative, high-visibility applications |
Choosing the Right Finish
The choice between e-coating and powder coating depends on the desired aesthetic and functional outcomes.
E-coating suits projects requiring precision and subtlety, while powder coating creates bold, eye-catching designs.
NOTE: For projects combining intricate designs with vibrant finishes, consider using e-coating as a base layer and powder coating as the topcoat. This approach enhances both durability and visual appeal.
Understanding each method's aesthetic preferences and finish options ensures the final product meets functional and design expectations.
Industry Applications of E-Coating and Powder Coating
Automotive Industry: Enhancing Longevity
The automotive industry depends on both e-coating and powder coating to enhance the durability and performance of vehicle components.
E-coating provides superior corrosion resistance, ensuring that parts like car bodies, frames, and chassis components remain rust-free even in harsh environments.
Its ability to coat hard-to-reach areas makes it ideal for intricate automotive designs. For example, suspension systems and brake calipers benefit from the uniform coverage provided by e-coating, which protects them from moisture and road salt.
Powder coating also plays a vital role in the automotive sector. It delivers a thick, durable finish that resists chipping and scratching, perfect for high-impact areas like wheels, bumpers, and grilles.
Additionally, powder coating enhances the aesthetic appeal of vehicles by offering vibrant colors and finishes.
This combination of durability and visual appeal ensures that automotive parts maintain their functionality and appearance over time.
Coating Type |
Applications |
Key Benefits |
E-Coating |
Car bodies, frames, suspension parts |
Corrosion resistance, uniform coverage, and protection in hard-to-reach areas. |
Powder Coating |
Wheels, bumpers, grilles |
Scratch resistance, vibrant finishes, and durability in high-impact environments. |
NOTE: E-coating often serves as a base layer for powder coating, combining the strengths of both methods for optimal protection and longevity.
Construction and Architecture: Durable Coatings
In construction and architecture, e-coating and powder coating provide essential protection for metal components exposed to outdoor elements.
E-coating offers excellent corrosion resistance, making it suitable for structural elements like steel beams and metal connectors.
Its ability to coat intricate shapes ensures that even the smallest parts receive complete protection, which is crucial for maintaining the integrity of buildings and infrastructure.
Powder coating enhances the durability and aesthetic appeal of architectural materials. It creates a tough, weather-resistant layer that protects against UV radiation, moisture, and physical damage.
Metal façades, railings, and window frames benefit from the powder coating’s ability to resist fading and erosion, ensuring that buildings keep their appearance and structural integrity.
- E-Coating Applications:
- Steel reinforcements
- Metal brackets and connectors
- Intricate architectural details
- Powder Coating Applications:
- Window and door frames
- Railings and fences
- Roofing panels and light poles
Combining these coatings ensures construction materials withstand environmental challenges while maintaining their functionality and visual appeal.
Consumer Goods: Everyday Durability
E-coating and powder coating contribute to the durability and longevity of many consumer goods.
E-coating provides a smooth, protective finish for jewelry, eyeglass frames, and small appliances. Its corrosion resistance ensures these products remain functional and visually appealing, even with frequent use.
Powder coating enhances the durability of larger consumer goods, such as furniture and home appliances. It creates a scratch-resistant surface that protects against wear and tear, making it ideal for refrigerators, washing machines, and metal chairs.
Additionally, powder coating offers various colors and finishes, allowing manufacturers to create durable and stylish products.
Product Type |
Coating Method |
Benefits |
Jewelry and Eyeglasses |
E-Coating |
Corrosion resistance and a smooth, durable finish. |
Home Appliances |
Powder Coating |
Scratch resistance, vibrant finishes, and protection against daily wear. |
Furniture |
Powder Coating |
Enhanced durability and aesthetic appeal for metal chairs and tables. |
NOTE: Powder coating’s eco-friendly process aligns with the growing demand for sustainable consumer products.
E-coating and powder coating ensure that consumer goods remain reliable and visually appealing, meeting the needs of both manufacturers and end-users.
Specialized Applications: Aerospace and Heavy Equipment
E-coating and powder coating are critical in the aerospace and heavy equipment industries. These sectors demand coatings that provide unmatched durability, corrosion resistance, and performance under extreme conditions.
Both methods ensure that components withstand harsh environments while maintaining their structural integrity.
Aerospace Industry: Precision and Protection
The aerospace industry relies on coatings to protect aircraft components from corrosion, wear, and environmental stress.
E-coating offers a thin, uniform layer that shields intricate parts from moisture, chemicals, and temperature fluctuations.
This precision makes it ideal for coating small, detailed components such as:
- Landing Gear Assemblies: E-coating prevents rust and wear caused by exposure to rain, snow, and de-icing chemicals.
- Cabin Interiors: The smooth finish enhances durability while maintaining a lightweight structure.
- Structural Components: E-coating ensures long-lasting protection for critical parts exposed to high altitudes and varying pressures.
Powder coating contributes to aerospace durability by providing a thicker, more robust finish. It protects larger components like:
- Engine Casings: The coating resists heat and physical damage, ensuring reliable performance.
- Exterior Panels: Powder coating shields against UV rays and weathering, preserving the aircraft’s appearance and functionality.
Coating Type |
Applications |
Key Benefits |
E-Coating |
Landing gear, cabin interiors, structural parts |
Corrosion resistance, lightweight finish, and uniform coverage. |
Powder Coating |
Engine casings, exterior panels |
Heat resistance, UV protection, and enhanced durability. |
NOTE: Combining e-coating for intricate parts with powder coating for larger surfaces ensures comprehensive protection across the aircraft.
Heavy Equipment: Strength and Longevity
Heavy equipment operates in demanding environments, constantly exposed to dirt, moisture, and physical stress.
E-coating provides a reliable solution for protecting smaller, intricate components such as:
- Hydraulic Cylinders: The coating prevents rust and wear, ensuring smooth operation.
- Fasteners and Bolts: E-coating shields these critical parts from corrosion, extending their lifespan.
With its thicker and more durable finish, powder coating is better suited for larger, high-impact components. Common applications include:
- Excavator Buckets: The coating resists scratches and dents caused by heavy use.
- Chassis Frames: Powder coating protects against moisture and chemicals, ensuring structural integrity.
Coating Type |
Applications |
Key Benefits |
E-Coating |
Hydraulic cylinders, fasteners |
Corrosion resistance and protection for intricate parts. |
Powder Coating |
Excavator buckets, chassis frames |
Scratch resistance, chemical protection, and durability under heavy use. |
Both coatings enhance the performance and longevity of heavy equipment, reducing maintenance costs and downtime.
Their ability to withstand extreme conditions makes them indispensable for construction, agriculture, and mining industries.
NOTE: For heavy-duty applications, powder coating’s thicker layer provides superior protection against physical damage, while e-coating safeguards smaller, detailed parts.
E-coating and powder coating ensure that aerospace and heavy equipment components remain durable and reliable, even in the most challenging environments.
Their specialized applications highlight their importance in industries where performance and longevity are paramount.
Maintaining E-Coated and Powder-Coated Surfaces
Best Practices for E-Coated Surfaces
E-coated surfaces require minimal maintenance to retain their durability and performance.
Following a few essential practices ensures long-term protection and quality.
Aspect |
Description |
Maintenance Needs |
E-coating requires minimal upkeep, reducing the need for frequent touch-ups or reapplications. |
Long-term Performance |
Durable finishes from e-coating provide sustained protection without compromising quality. |
Quality Control |
Regular inspections ensure high standards, maintaining the integrity and performance of coated parts. |
Corrosion Prevention |
Consistent quality control minimizes corrosion risks, extending the lifespan of components. |
To maintain e-coated surfaces effectively:
- Inspect surfaces periodically for signs of wear or damage.
- Clean with a soft cloth and mild detergent to remove dirt and debris.
- Avoid abrasive cleaning tools that could scratch the coating.
- Store e-coated items in dry, controlled environments to prevent unnecessary exposure to moisture.
These practices ensure that e-coated surfaces remain functional and visually appealing.
Best Practices for Powder-Coated Surfaces
Powder-coated surfaces benefit from regular care to preserve their durability and appearance.
Proper cleaning and protection methods help maintain their integrity.
- Clean surfaces regularly using mild soap and warm water. Ensure the soap is pH-neutral to avoid damaging the coating.
- Use low-pressure cleaning methods with filtered water to prevent staining or surface damage.
- Apply a wax coating to areas that experience frequent contact or wear, which adds an extra layer of protection against UV rays and physical stress.
- Avoid harsh cleaning agents or abrasive tools, which may compromise the finish.
NOTE: Treat powder-coated surfaces like a car’s paint job. Just as waxing a car protects it from the elements, applying wax to powder-coated surfaces enhances its longevity.
Regular maintenance keeps powder-coated surfaces looking new and doubles their lifespan.
Extending the Lifespan of Coated Materials
Both e-coating and powder coating significantly enhance the durability of materials.
However, proper care ensures these coatings perform at their best for years.
E-coating provides a uniform finish that protects even the most complex shapes.
This coverage reduces the risk of corrosion and abrasion, extending the life cycle of coated products.
With its thicker layer, powder coating offers robust protection against physical damage and environmental factors.
To maximize the lifespan of coated materials:
- Clean surfaces regularly to remove contaminants that may degrade the coating.
- Use the correct cleaning methods, such as low-pressure water or soft cloths, to avoid damaging the finish.
- Inspect coatings periodically for chips or scratches and address them promptly to prevent further deterioration.
- Store coated items in environments that minimize exposure to extreme temperatures, moisture, or UV radiation.
NOTE: Proper maintenance practices double or triple the effective service life of e-coated and powder-coated materials.
By following these guidelines, manufacturers, and end-users ensure coated surfaces remain durable, functional, and visually appealing for extended periods.
Future Innovations in Coating Technology
Advancements in E-Coating
E-coating technology continues to evolve, offering enhanced durability and efficiency.
Recent advancements focus on improving corrosion resistance and adhesion while reducing waste.
These innovations ensure that coated surfaces remain protected in challenging environments.
- Uniform Coating: E-coating creates a consistent layer that shields metal surfaces from rust and corrosion. This uniformity enhances the longevity of industrial machinery and automotive parts.
- Superior Adhesion: The process ensures that the coating bonds tightly to the metal, providing complete protection for intricate designs and hard-to-reach areas.
- Cost-Effectiveness: E-coating reduces material waste, making it an economical choice for large-scale applications.
Industries rely on rigorous testing methods to measure the effectiveness of these advancements:
- Salt Spray Test: Simulates harsh conditions to evaluate corrosion resistance.
- Gravelometer Test: Assesses the coating's ability to withstand impact and abrasion.
- Adhesion Test: Verifies the strength of the bond between the coating and the metal surface.
- Thickness Measurement: Ensures consistent coating thickness for optimal performance.
These innovations make e-coating a reliable solution for industries requiring durable and sustainable finishes.
Advancements in Powder Coating
Powder coating technology has also seen significant progress, particularly in enhancing durability and finish quality.
Modern techniques allow for thicker coatings without sagging or running, ensuring a smooth and uniform appearance.
The electrostatic application process plays a key role in these advancements. It improves adhesion and consistency, resulting in coatings that resist UV light, chemicals, and abrasion.
This durability makes powder coating ideal for outdoor and industrial applications.
New formulations offer better protection against environmental factors.
For example, UV-resistant powders prevent fading and degradation, while chemical-resistant coatings protect surfaces in harsh industrial settings.
These improvements ensure that powder-coated materials maintain their functionality and appearance over time.
Sustainability Trends in Coating Processes
Sustainability has become a driving force in the development of coating technologies.
Emerging materials and processes aim to reduce environmental impact while maintaining durability.
- Bio-based Coatings: Materials like cellulose and seaweed-derived alkyd resins are gaining popularity. Cellulose improves coatings' thermal and mechanical properties, while seaweed-based resins offer durability and cost-effectiveness.
- Non-Toxic Solutions: Cellulose-based coatings are biodegradable and non-toxic, making them an eco-friendly alternative to traditional materials.
- Reduced Waste: Both e-coating and powder coating minimize waste during application, aligning with sustainability goals.
These trends highlight the industry's commitment to balancing performance with environmental responsibility.
By adopting sustainable practices, manufacturers ensure coatings remain durable while reducing their ecological footprint.
NOTE: Integrating sustainable materials benefits the environment and enhances coatings' overall performance, making them a win-win solution for industries worldwide.
E-coating and powder coating play vital roles in enhancing the durability of materials across industries.
Each method offers distinct advantages tailored to specific needs.
- E-Coating excels in corrosion resistance and uniform coverage, making it ideal for intricate designs and harsh environments.
- Powder Coating provides a thicker, impact-resistant finish with a wide range of aesthetic options, perfect for outdoor and high-traffic applications.
Understanding these strengths allows manufacturers to select the most suitable solution based on application requirements, material type, and environmental conditions.
This informed approach ensures long-lasting protection, reduced maintenance, and optimal performance for coated products.
Key Takeaways
- E-coating stops rust, making it great for small metal parts in tough conditions.
- Powder coating creates a thick, strong layer that avoids scratches, chips, and sun damage, ideal for outdoor use.
- Both e-coating and powder coating are safe for the environment, with little waste and no harmful chemicals.
- E-coating works well on tricky shapes and tight spots, giving even coverage and protection.
- Powder coating offers many colors and styles, making products look better.
- Cleaning coated surfaces gently helps them last longer and look nice.
- Using both e-coating and powder coating together makes items stronger and more attractive.
- Industries like cars, planes, and buildings use these coatings for long-lasting results.