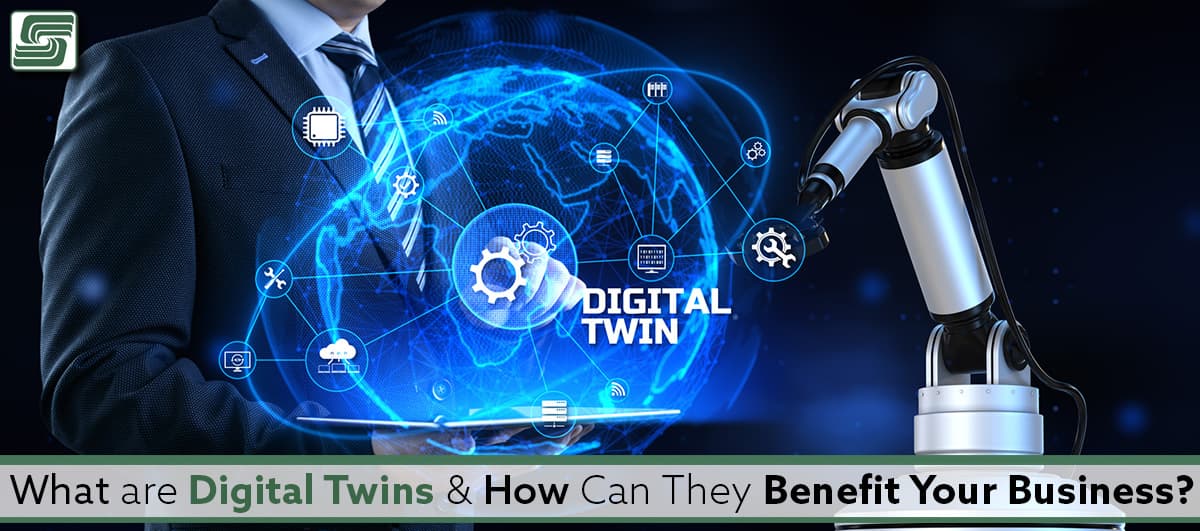
Manufacturing is an industry that has long struggled to keep pace with the rapid rate of change in other sectors.
While e-commerce and artificial intelligence have drastically reshaped how consumers interact with brands and make products, the manufacturing process has remained essentially the same for decades.
In fact, a report from McKinsey revealed that just 6% of manufacturing companies worldwide had adopted digital technologies as of 2016, compared to over 75% of services businesses.
This lag in adoption is partially because of the unique challenges posed by the physical nature of factories, but it's also because manufacturers have been slow to adopt new technologies. However, this is thankfully changing.
An increased focus on Industry 4.0 — a transformation towards data-driven production processes driven by cyber-connected machines, devices, people, and software — has helped speed up the adoption of new digital solutions in manufacturing.
And manufacturers can start taking advantage of these transformative trends by using Digital Twins in the manufacturing processes.
What is a Digital Twin?
A digital twin is a computer-based model with as much information as possible about one particular object or process. It can better understand and optimize an object's or process's performance.
For example, the digital twin of a factory machine has all the information needed to run the equipment, such as operating hours, maintenance schedules, and energy use, by integrating this information with other digital assets, such as the factory's layout and the production process.
We can visualize all of this data in a digital simulation, allowing stakeholders to make more informed decisions.
More broadly speaking, a digital twin is an online representation of a physical product or process. They often describe it as having a "digital DNA" used to integrate data from other sources such as sensors, the Internet of Things (IoT), and other data sources to create a more holistic picture of how a product or process is performing.
Why Use Digital Twins in Manufacturing?
Digital Twins not only help manufacturers improve their production processes but also enables them to offer new and improved customer experiences.
The benefits of deploying Digital Twins in manufacturing include:
- Better understanding of production processes: Digital Twins create visual representations of the production process, helping manufacturers understand where they could improve.
- Real-time insights: Integrating data from sensors, machines, and other assets will allow manufacturers to make more informed decisions and see real-time insights into the production process.
- More informed decisions: Sharing Data across the entire supply chain, making it easier to collaborate and make better decisions based on a 360-degree view of the production process.
- Improved customer experience: Digital Twin technology creates a digital representation of a product that customers can access. In the B2B realm, this could include things like how to deliver a service to clients.
3 Things You Can Do With a Digital Twin
- Create Virtual Prototypes: By visualizing the production process and testing how the design looks in the real-world environment, you can save time and money by identifying potential issues early on.
- Streamline Collaboration: Digital Twins help improve collaboration across teams and departments by making it easier to share information and make decisions.
- Improve Resource Utilization: Digital Twins help you better understand the utilization of your resources by helping you make more informed decisions regarding resourcing and staffing.
Automate Tasks with Robotics and AI
One of the biggest challenges facing manufacturing companies today is the growing shortage of skilled workers. However, introducing robotics and AI into the production process helps address this issue and allows manufacturers to increase production capacity.
For example, by creating the production process simulation described above, manufacturers can better understand applying robotics and AI.
Using machine learning and artificial neural networks, we can program machines to learn how to perform tasks without requiring a human being to be in the loop.
Improve Resource Utilization with Real-time Data
Manufacturers often struggle to optimize the use of all the resources at their disposal. With Digital Twins, you can make more informed decisions about how and when to use each resource to achieve a more balanced production level, such as energy consumption and water usage.
While this data has historically been challenging, it's now available through IoT technologies, such as sensors. This real-time data allows you to make more informed decisions about using resources in your organization.
Monitor Everything
One of the manufacturers' biggest challenges today is identifying when something goes wrong — especially with production. Digital Twins help with this in a few ways:
- Monitor Key Assets: By creating a digital representation of your critical assets, you can track their health and performance, identify maintenance times, and help avoid costly repair work.
- Measure Process Performance: Integrating data from sensors and machines allows you to measure the performance of the production process, helping identify when something goes wrong and enabling you to respond accordingly.
In Sum
The manufacturing industry has slowly adapted to the digital transformation sweeping other sectors. The rise of the Internet of Things and the adoption of Industry 4.0 allows manufacturers to revolutionize their business.
They can take advantage of these transformative trends by deploying Digital Twins throughout their organization. Digital Twins not only allow manufacturers to understand their production processes better, but they also help them improve resource utilization. Digital Twins also enable manufacturers to monitor their critical assets and perform better.