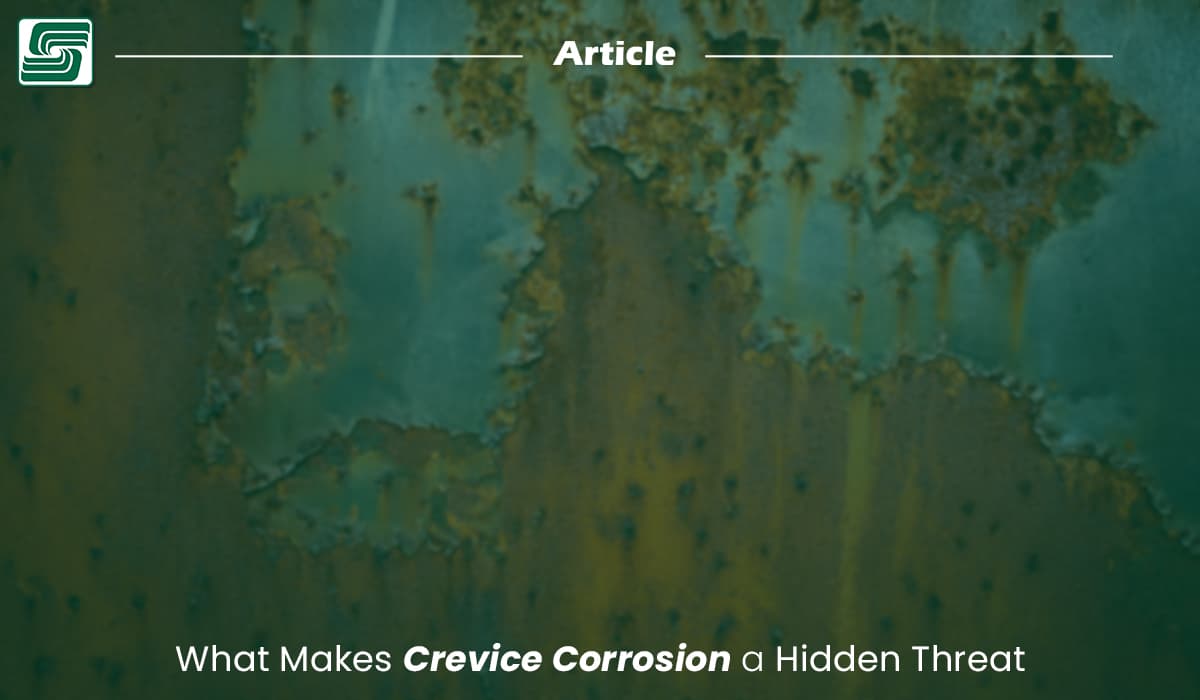
Crevice corrosion is like a hidden leak in your roof—it starts small and out of sight in places you rarely check, like under shingles or around seals. Similarly, it develops in tight spaces such as gaps between metal parts, under gaskets, or beneath layers of debris. At first, the damage is quiet and barely noticeable, making it hard to catch before it becomes a bigger problem.
Over time, this localized corrosion weakens the material, leading to structural failures. Its hidden nature makes it one of the most dangerous forms of corrosion, especially in critical applications.
Crevice corrosion is like a hidden leak in a boat—working quietly and unnoticed, slowly weakening what you rely on. When you see the signs, the damage is already severe, like a leak that flooded the lower deck. This silent, persistent nature makes crevice corrosion a stealthy adversary, posing a serious risk to the strength and durability of your equipment and structures. Recognizing its subtle beginnings is key to preventing costly surprises down the line.
Why Crevices Create Stagnant Micro-Environments
Crevices are like tiny caves where trouble hides. They trap moisture, dirt, and corrosive substances like a cave holding onto damp air and grime. Because airflow can't reach these tight spaces, the air inside runs out of breath and becomes stale. This stale environment sets the perfect stage for corrosion to grow as mold thrives in a damp, closed closet.
Stagnant microenvironments are like little puddles that never dry up. Over time, harmful chemicals, like chlorides, build up in these puddles, just as salt concentrates in water that evaporates slowly. These concentrated chemicals attack the metal surface aggressively, like acid eating away at a stone. Since nothing moves in these tight spots, there's no way to rinse away the damage, making the corrosion worse and faster.
The Consequences of Undetected Corrosion
Undetected crevice corrosion is a serious concern that leads to significant risks in various industrial applications. This type of corrosion occurs in small, confined spaces where moisture and other corrosive agents accumulate, creating an environment that deteriorates materials. As a result, these materials' structural integrity and durability are compromised, increasing the likelihood of unexpected failures.
Failures occur in various forms, such as leaking pipes, malfunctioning equipment, and severe incidents like explosions or environmental disasters. Their unpredictability presents safety hazards to personnel and the surrounding environment and disrupts operations.
Crevice corrosion is like a hidden crack in the foundation of a house—it causes big problems if ignored. This unseen damage leads to expensive repairs and delays for companies, like fixing a crumbling foundation, disrupting daily life. Businesses might face legal troubles if the problem leads to accidents or environmental harm, piling onto losses. Catching and addressing crevice corrosion early is like sealing that crack before it spreads—essential for keeping operations safe, reliable, and financially secure.
Ignoring crevice corrosion also jeopardizes safety. Structural failures caused by corrosion endanger lives, especially in the aerospace, marine, and chemical processing industries. When you notice the damage, the cost of addressing it may already be substantial. Understanding the hidden nature of crevice corrosion helps you take proactive measures to prevent these consequences.
What Is Crevice Corrosion?
Crevice corrosion refers to a localized form of corrosion that occurs in confined spaces or gaps between the two surfaces. These spaces often trap moisture, debris, and other corrosive substances. The restricted environment inside the crevice accelerates the breakdown of metal. This type of corrosion typically develops in areas where two materials meet but do not fit perfectly, such as bolted joints, gaskets, or overlapping surfaces.
Crevice corrosion targets specific areas, unlike general corrosion, which spreads evenly across a surface. This focused attack weakens the material in those spots, making it a serious concern for structural integrity. You might encounter this issue in environments with stagnant water or aggressive ions, like chlorides.
What are the Key Characteristics of Crevice Corrosion?
Several features make crevice corrosion distinct and dangerous. First, it often begins in areas that are difficult to inspect or access. These hidden locations allow the damage to progress unnoticed. Second, it thrives in stagnant environments where oxygen levels drop. This oxygen depletion creates an imbalance that promotes the accumulation of corrosive agents.
Another characteristic is its rapid progression once it starts. The confined space traps harmful substances, intensifying the attack on the metal. If the corrosion becomes visible, you may notice pitting or localized damage. However, by the time you detect it, significant material loss might have already occurred.
Why is it Different from Other Forms of Corrosion?
Crevice corrosion differs from other types of corrosion in several ways. General corrosion affects the entire surface of a material, while crevice corrosion targets specific, confined areas. Pitting corrosion, another localized form, occurs on open surfaces, whereas crevice corrosion develops in hidden gaps or overlaps.
The conditions that lead to crevice corrosion also set it apart. It requires a stagnant environment with limited oxygen and aggressive ions, creating a unique micro-environment that accelerates corrosion. Understanding these differences helps you identify and address crevice corrosion more effectively.
The Stages of Crevice Corrosion
Stage |
Description |
Key Effects |
Stage 1: Oxygen Depletion |
Oxygen levels drop in confined spaces like gaps or under deposits. Without oxygen, the protective oxide layer weakens. |
Creates an imbalance where inside the crevice becomes oxygen-depleted and vulnerable to damage. |
Stage 2: Ion Concentration |
Aggressive ions like chlorides build up, creating an acidic environment. Trapped ions intensify the damage. |
Accelerates corrosion as acid attacks the exposed metal surface in the confined space. |
Stage 3: Metal Dissolution |
The metal dissolves due to an acidic environment and concentrated ions, causing localized damage. |
Weakens material, spreads damage, and compromises structural integrity, often unnoticed. |
Stage 1: Oxygen Depletion in Confined Spaces
Crevice corrosion begins when oxygen levels drop in confined spaces. These spaces, such as gaps between metal surfaces or under deposits, restrict airflow. Without sufficient oxygen, the protective oxide layer on the metal surface weakens. This layer usually shields the metal from corrosive elements. Its breakdown exposes the underlying material to potential damage.
The lack of oxygen creates an imbalance between the crevice and the surrounding environment. Outside the crevice, oxygen remains available, maintaining a stable condition. Inside the crevice, however, the oxygen-depleted zone becomes vulnerable. This imbalance sets the stage for the next phase of corrosion.
Stage 2: Ion Concentration and Aggressive Environments
As oxygen levels drop, the environment inside the crevice changes. Aggressive ions, such as chlorides, accumulate. These ions often come from the surrounding environment, including seawater, industrial chemicals, or cleaning agents. Their concentration increases because the confined space traps them, preventing dilution.
The buildup of these ions creates an acidic environment. This acidity accelerates the corrosion process by attacking the exposed metal surface. The confined space amplifies the damage, as the trapped ions cannot escape. This stage marks a critical point where the corrosion process intensifies rapidly.
Stage 3: Metal Dissolution and Localized Damage
In the final stage, the metal within the crevice dissolves. The acidic environment and concentrated ions break down the metal at a microscopic level. This dissolution weakens the material, leading to localized damage. Over time, the damage spreads, compromising the structural integrity of the affected area.
The crevice's confined nature prevents natural cleaning or repair. The damage remains hidden, making it difficult to detect. By the time visible signs appear, the material may already have suffered significant loss. This stage highlights the destructive potential of crevice corrosion when left unchecked.
Why Crevice Corrosion Progresses Undetected
Crevice corrosion is like a silent invader hiding in the shadows, often going unnoticed until significant damage is done. It thrives in small, hard-to-reach spaces, like the tiny gaps between bolted joints or overlapping surfaces, where routine inspections rarely venture. Picture it as a slow leak behind a wall—you don’t see the problem until the damage becomes obvious.
Unlike general corrosion, which spreads openly across a surface like rust covering a fence, crevice corrosion is more like a sniper targeting specific weak points. It works in secret, its localized assault hidden until it reveals itself through issues like leaks or structural failures, much like discovering termites after they’ve hollowed out your floorboards.
This stealthy process doesn’t leave clear warning signs. It’s not like general wear and tear that shows as rust stains or rough patches. Instead, crevice corrosion operates quietly, giving no hints until the problem becomes severe. When it’s visible, repairing the damage may be as complex as restoring a crumbling foundation. Recognizing its secretive nature highlights why proactive prevention is essential to keep this hidden threat in check.
Where Does Crevice Corrosion Typically Occur?
Common Locations in Industrial Applications
Location |
Description |
Preventive Actions |
Bolted Joints and Fasteners |
Small gaps trap moisture, dirt, and corrosive substances. Restricted airflow depletes oxygen, promoting localized corrosion. |
Conduct regular inspections of bolted connections to identify early signs of corrosion. |
Gaskets, Seals, and Overlapping Surfaces |
Narrow spaces collect stagnant water or corrosive chemicals, accelerating metal breakdown. This is common in environments with aggressive ions like chlorides. |
Pay close attention to these areas during maintenance, especially in harsh environments. |
Under Deposits or Biofilms |
Accumulated deposits or biofilms block oxygen, creating stagnant micro-environments that intensify corrosion. |
Regularly clean metal surfaces to remove deposits and biofilms. |
Welded Joints |
Residual stress and material inconsistencies can trap corrosive agents. |
Inspect welds for trapped contaminants and apply protective coatings. |
Riveted Connections |
Similar to bolts, rivets can form crevices where corrosion starts. |
Check riveted areas for gaps and maintain protective finishes. |
Heat Exchanger Tubes |
Gaps between tubes and tube sheets can retain water or chemicals. |
Ensure proper cleaning and flushing during maintenance cycles. |
Valve Interiors |
Small voids within valve assemblies can lead to corrosion. |
Disassemble and inspect valves periodically to prevent internal corrosion. |
Bolted Joints and Fasteners
Bolted joints and fasteners often create small gaps where crevice corrosion develops. These areas trap moisture, dirt, and other corrosive substances. The tight spaces between the bolt and the surrounding material restrict airflow, leading to oxygen depletion. This lack of oxygen promotes localized corrosion. Regular inspections of bolted connections help identify early signs of damage.
Gaskets, Seals, and Overlapping Surfaces
Gaskets, seals, and overlapping surfaces provide ideal conditions for crevice corrosion. These components often form narrow spaces that collect stagnant water or corrosive chemicals. The trapped substances accelerate the breakdown of metal surfaces. During maintenance, pay close attention to these areas, especially in environments exposed to aggressive ions like chlorides.
Under Deposits or Biofilms
Deposits or biofilms that accumulate on metal surfaces also contribute to crevice corrosion. These layers block oxygen from reaching the metal, creating a stagnant micro-environment. The trapped debris or organic matter fosters conditions that intensify corrosion. Regularly cleaning these surfaces reduces the risk of damage and extends the lifespan of your equipment.
Other Locations to Monitor
- Welded joints: Residual stress and material inconsistencies trap corrosive agents.
- Riveted connections: Like bolts, rivets form crevices where corrosion starts.
- Heat exchanger tubes: Gaps between tubes and tube sheets keep water or chemicals.
- Valve interiors: Small voids within valve assemblies lead to corrosion.
Industries Most at Risk
Marine and Offshore Environments
Marine and offshore environments face significant risks because of constant exposure to saltwater. The high chloride content in seawater accelerates crevice corrosion, especially in confined spaces. Bolted joints, gaskets, and other components in marine structures require careful monitoring. In these settings, prioritize corrosion-resistant materials and protective coatings.
Aerospace Components
Aerospace components often experience extreme conditions, including temperature fluctuations and exposure to moisture. These factors increase the likelihood of crevice corrosion in critical areas like fasteners and overlapping surfaces. Regular inspections and the use of advanced materials help mitigate risks in this industry.
Chemical Processing Equipment
Chemical processing equipment operates in environments filled with aggressive chemicals and high humidity. These conditions create ideal scenarios for crevice corrosion, making gaskets, seals, and areas under deposits vulnerable. Selecting materials resistant to chemical attacks and maintaining a strict cleaning schedule minimizes potential damage.
What Factors Contribute to Crevice Corrosion?
Metals Prone to Crevice Corrosion
Some metals are more vulnerable to crevice corrosion than others. Stainless steel, for example, often experiences this issue despite its corrosion-resistant reputation. The protective oxide layer on stainless steel fails in confined spaces, exposing the metal to damage. Aluminum and titanium alloys also face similar risks in specific environments. When selecting materials, consider their susceptibility to localized corrosion, especially in applications involving tight gaps or stagnant conditions.
The Role of Protective Coatings
Protective coatings play a crucial role in reducing the risk of crevice corrosion. These coatings act as a barrier, shielding the metal surface from corrosive substances. However, improper application or damage to the coating leaves the underlying material exposed. You should ensure that coatings are applied evenly and inspected regularly. Using advanced coating technologies enhances durability and provides better protection in challenging environments.
Environmental Conditions
The Impact of Chlorides and Aggressive Ions
Chlorides and other aggressive ions significantly accelerate crevice corrosion. These ions often come from seawater, industrial chemicals, or cleaning agents. In confined spaces, they concentrate and create an acidic environment that attacks the metal surface. If your equipment operates in chloride-rich environments, take extra precautions. Selecting materials resistant to chloride-induced corrosion and maintaining a strict cleaning routine helps mitigate these risks.
High Humidity and Stagnant Water
High humidity and stagnant water create ideal conditions for crevice corrosion. Moisture trapped in confined spaces depletes oxygen levels, disrupting the protective oxide layer on metals. Stagnant water further exacerbates the problem by allowing corrosive substances to accumulate. You should address areas prone to water retention and ensure proper drainage. Regular inspections and drying procedures help reduce the impact of these environmental factors.
Design and Geometry
The Role of Tight Gaps and Poor Drainage
Tight gaps and poor drainage contribute significantly to crevice corrosion. Narrow spaces trap moisture and debris, creating a stagnant environment where corrosion thrives. Poor drainage allows water to collect, increasing the likelihood of damage. When designing equipment, you should minimize tight crevices and incorporate features that promote proper drainage. These design improvements reduce the risk of localized corrosion.
How Surface Roughness Affects Corrosion
Surface roughness influences the development of crevice corrosion. Rough surfaces provide more opportunities for debris and moisture to accumulate. These irregularities create micro-crevices that foster stagnant conditions. You should prioritize smooth finishes for components exposed to corrosive environments. Polished surfaces reduce the likelihood of crevice formation and improve the overall corrosion resistance.
Preventing Crevice Corrosion
Avoiding Tight Crevices and Ensuring Drainage
Category |
Measure |
Description |
Benefits |
Avoiding Tight Crevices |
Design for Fewer Crevices |
Minimize narrow gaps that trap moisture and debris. |
Reduces the risk of stagnant conditions and corrosion. |
|
Ensure Proper Drainage |
Incorporate drainage systems to allow water and corrosive substances to flow away. |
Prevents accumulation of corrosive agents in confined spaces. |
Optimizing Surface Features |
Use Rounded Edges and Smooth Surfaces |
Eliminate sharp corners and rough finishes where moisture collects. |
Reduces micro-crevices, making cleaning easier and improving durability. |
Material Selection |
Choose Corrosion-Resistant Alloys |
Select materials like stainless steel or titanium that resist harsh environments. |
Offers durability against aggressive ions such as chlorides. |
|
Apply Protective Coatings and Surface Treatments |
Use barriers like coatings or advanced treatments (e.g., passivation, anodizing) to shield metal surfaces. |
Protects surfaces from moisture, debris, and corrosive ions. |
Maintenance Practices |
Perform Regular Cleaning |
Remove deposits like dirt, biofilms, or residues that block oxygen and accelerate corrosion. |
Maintains a balanced environment and restores protective oxide layers. |
|
Conduct Routine Inspections |
Regularly check bolted joints, gaskets, and overlapping surfaces for signs of corrosion. |
Enables early detection and prevents escalation of localized damage. |
Focus on designs that minimize tight crevices. Narrow gaps trap moisture and debris, creating the perfect environment for corrosion to develop. By eliminating these spaces, you reduce the risk of stagnant conditions. Incorporating proper drainage systems into your designs also helps. Drainage allows water and other corrosive substances to flow away, preventing them from accumulating in confined areas. These adjustments improve the durability and lifespan of your equipment.
Using Rounded Edges and Smooth Surfaces
Rounded edges and smooth surfaces play a critical role in reducing crevice corrosion. Sharp corners and rough finishes create micro-crevices where moisture and debris collect. By opting for rounded edges, you eliminate these vulnerable spots. Smooth surfaces make cleaning easier, ensuring that corrosive substances do not linger. Prioritizing these design features enhances the resistance of your equipment to localized corrosion.
Material Selection
Choosing Corrosion-Resistant Alloys
Selecting the right materials is essential for preventing crevice corrosion. Corrosion-resistant alloys, such as certain grades of stainless steel or titanium, offer better protection in harsh environments. These materials maintain their integrity even when exposed to aggressive ions like chlorides. When choosing alloys, consider the specific conditions your equipment will face. This proactive approach ensures that your materials withstand the challenges of their environment.
Applying Protective Coatings and Surface Treatments
Protective coatings and surface treatments act as barriers against corrosive elements. These layers shield the metal from moisture, debris, and aggressive ions. However, you must ensure that the coatings are applied evenly and inspected regularly. Any damage to the coating exposes the underlying material to corrosion. Advanced surface treatments, such as passivation or anodizing, further enhance the protective properties of your equipment. These measures significantly reduce the likelihood of localized damage.
Maintenance Practices
Regular Cleaning to Remove Deposits
Regular cleaning is vital for preventing crevice corrosion. Deposits, such as dirt, biofilms, or industrial residues, block oxygen from reaching the metal surface, creating stagnant conditions that accelerate corrosion. Removing these deposits restores the protective oxide layer and maintains a balanced environment. Use proper cleaning methods to avoid damaging the surface while thoroughly removing harmful substances.
Routine Inspections for Early Detection
Routine inspections help you identify early signs of crevice corrosion. Focus on areas prone to damage, such as bolted joints, gaskets, and overlapping surfaces. Look for discoloration, pitting, or other visible indicators of localized corrosion. Early detection allows you to address the issue before it escalates. Incorporating regular inspections into your maintenance schedule ensures the long-term reliability of your equipment.
Other Preventive Actions to Consider
- Stress Reduction: Reduce residual stress in metals through proper welding and machining practices to lower susceptibility.
- Environmental Controls: Use dehumidifiers or corrosion inhibitors in storage or operational environments.
- Cathodic Protection: Apply electrochemical protection systems where applicable.
The Risks of Ignoring Crevice Corrosion
Structural Failures and Safety Hazards
Ignoring crevice corrosion leads to serious structural failures. This localized corrosion weakens materials in hidden areas, such as bolted joints or under gaskets. Over time, the damage compromises the strength of critical components. Equipment or structures may fail unexpectedly, creating dangerous situations. These failures pose significant safety hazards in the marine, aerospace, or chemical processing industries. Protecting lives and ensuring operational safety requires addressing this hidden threat early.
Financial Costs of Repairs and Downtime
The financial impact of undetected crevice corrosion is substantial. When corrosion progresses unnoticed, repairs become more extensive and expensive. Replacing damaged components or entire systems increases costs significantly. Downtime caused by equipment failure disrupts operations, leading to lost productivity and revenue. Sometimes, businesses face additional expenses from liability claims or regulatory penalties. By understanding the risks, you can avoid these costly consequences and maintain efficient operations.
The Benefits of Proactive Measures
Extending Equipment Lifespan
Proactive measures against crevice corrosion help extend the lifespan of your equipment. Regular maintenance, inspections, and design improvements prevent damage before it starts. By addressing potential problem areas, you preserve the structural integrity of materials. This approach reduces wear and tear, allowing your equipment to perform reliably for longer periods. Investing in prevention ensures that your assets remain functional and durable.
Reducing Maintenance Costs and Improving Reliability
Preventing crevice corrosion lowers maintenance costs. Early detection and routine cleaning reduce the need for expensive repairs, so you spend less on replacing parts or dealing with unexpected failures. Proactive measures improve the reliability of your equipment. When components remain free from localized corrosion, they operate more efficiently. This reliability minimizes disruptions, enhances productivity, and builds confidence in your operations.
In Sum
Crevice corrosion remains a hidden threat that compromises the integrity of materials and structures. By understanding its causes and progression, you gain the knowledge to address this challenge effectively. Prevention starts with informed decisions about design, materials, and maintenance practices.
When you take proactive steps, you protect your equipment, reduce costs, and ensure safety. With the right strategies, managing the risks associated with crevice corrosion is achievable. With awareness and action, you safeguard your operations and extend the lifespan of critical assets.
Key Takeaways
- Crevice corrosion develops in hidden spaces, making it difficult to detect until significant damage occurs, which leads to structural failures.
- Stagnant micro-environments in crevices trap moisture and aggressive ions, accelerating corrosion and compromising material integrity.
- Regular inspections and maintenance of areas prone to crevice corrosion, such as bolted joints and gaskets, are essential for early detection and prevention.
- Choosing corrosion-resistant materials and applying protective coatings significantly reduce the risk of crevice corrosion in critical applications.
- Implementing design improvements, such as avoiding tight crevices and ensuring proper drainage, helps minimize the conditions that foster crevice corrosion.
- Proactive measures not only extend the lifespan of equipment but also reduce maintenance costs and improve overall reliability.
- Awareness of crevice corrosion risks ensures safety and prevents costly repairs in marine, aerospace, and chemical processing industries.