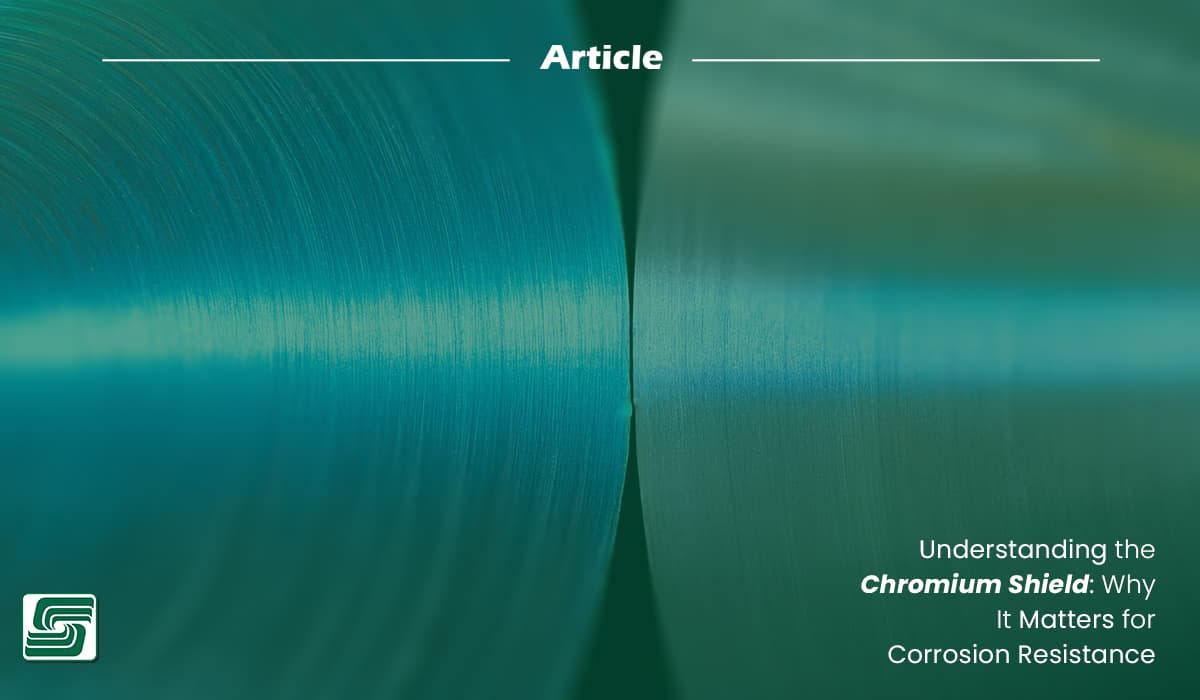
Corrosion resistance in metals holds immense importance because of its economic impact. Corrosion costs the U.S. economy approximately $276 billion annually. Understanding corrosion mechanisms is crucial for mitigating these expenses. The chromium shield plays a vital role in enhancing corrosion resistance.
Chromium forms a protective oxide layer on stainless steel, preventing damage from corrosive elements. Grade stainless steel, containing chromium, offers superior corrosion resistance. This protection ensures longevity and durability in various environments.
Recognizing the significance of the chromium shield aids in selecting the right grade stainless steel for specific applications.
The Science Behind Corrosion
Corrosion is the natural process by which metals deteriorate from chemical reactions with their environment.
This process involves transforming metal into more stable compounds, such as oxides or sulfides. Corrosion weakens metals' structural integrity, leading to potential failures.
Common Types of Corrosion
Metals experience various types of corrosion, including:
- Uniform Corrosion Occurs evenly across the surface, causing consistent metal thinning.
- Pitting Corrosion: Localized attacks create small holes or pits, often leading to severe damage.
- Galvanic Corrosion: Occurs when two different metals are in contact in a corrosive environment, leading to the accelerated corrosion of one metal.
- Crevice Corrosion: Occurs in confined spaces where the solution becomes stagnant.
The Role of Chromium in Corrosion Resistance
Chromium plays a crucial role in enhancing stainless steel's corrosion resistance. When exposed to oxygen, chromium reacts to form a thin, protective layer of chromium oxide on the surface.
This layer acts as a barrier, preventing further oxidation and corrosion of the underlying metal.
How Chromium Enhances Durability
Chromium's ability to form a self-healing oxide layer ensures long-lasting protection. If the layer gets damaged, chromium quickly reforms the oxide in the presence of oxygen.
This property makes stainless steel, especially the 200-300 series stainless steel, highly durable in various environments.
- Higher chromium content leads to improved passivation potential.
- The chromium oxide film blocks chemical reactions with oxygen, reducing corrosion.
Stainless steel alloys, including the ASTM series, rely on chromium for their exceptional corrosion resistance. The 200-300 series stainless steel grades are particularly noted for their robust performance because of optimal chromium content.
Factors Affecting Stainless Steel Corrosion Resistance
Factor |
Description |
Environmental Factors |
Humidity and Temperature |
Higher humidity and temperature accelerate corrosion due to increased formation of corrosive agents and faster chemical reactions. |
Chemical Exposure |
Certain chemicals can react aggressively with stainless steel, compromising the protective chromium oxide layer. Acidic or alkaline environments demand stainless steel alloys with enhanced corrosion resistance. |
Material Composition |
Chromium Content |
Higher chromium levels enhance the formation of a stable oxide layer, providing better corrosion resistance. |
Role of Other Alloying Elements |
Nickel, molybdenum, and nitrogen improve corrosion resistance and enhance the stability of the passive film. |
Comparative Data |
Manufacturer Variation |
316 stainless steel corrosion rates can vary between manufacturers. Coatings like Dursan® can help equalize these rates. |
Corrosion Morphology |
2205 DSS and 316L SS show different corrosion morphologies under different conditions. |
Austenitic Stainless Steel |
Austenitic stainless steels generally have lower corrosion resistance than 304 and 316 due to passive film instability. |
Stainless steel alloys designed for specific applications must consider these factors, and the right choice ensures optimal performance and extended service life.
Types of Stainless Steel and their Corrosion Resistance
Type |
Composition |
Properties |
Corrosion Resistance |
Austenitic Stainless Steel |
High chromium and nickel |
Non-magnetic, strong at high/low temperatures |
Excellent corrosion resistance, resists pitting/crevice corrosion, resists chloride-rich environments (with molybdenum) |
Ferritic Stainless Steel |
High chromium, no nickel |
Magnetic, formable |
Good corrosion resistance, resists stress corrosion cracking, may not perform as well in highly corrosive environments |
Martensitic Stainless Steel |
Moderate chromium and carbon |
High strength and hardness |
Lower corrosion resistance than other types, susceptible to corrosion in humid environments or with corrosive chemicals |
These alloys belong to the 400 series and are known for their good corrosion resistance and formability.
Common applications include
- Automotive Exhaust Systems
- Industrial Equipment
- Kitchenware
Martensitic stainless steels contain moderate chromium and carbon levels. These alloys exhibit high strength and hardness, making them suitable for applications requiring wear resistance.
The 400 series also include martensitic types, often used in:
- Cutlery
- Surgical Instruments
- Turbine Blades
However, these metals offer lower corrosion resistance than their austenitic and ferritic counterparts.
Corrosion Resistance Comparison
Because of their chromium content, ferritic stainless steels provide decent corrosion resistance, although they may not perform as well as austenitic alloys in highly corrosive environments.
The absence of nickel limits their ability to withstand certain chemical exposures. However, ferritic steels resist stress corrosion cracking, making them suitable for specific applications where this issue is a concern.
While strong and durable, martensitic stainless steels exhibit lower corrosion resistance than other stainless-steel types. The higher carbon content increases susceptibility to corrosion, especially in environments with high humidity or exposure to corrosive chemicals.
Proper maintenance and protective coatings help extend the lifespan of martensitic metal parts.
Processes Enhancing Corrosion Resistance
Process |
Description |
Benefits |
Passivation |
Treats stainless steel to form a protective chromium oxide layer |
Enhances corrosion resistance, prevents rust, improves longevity, ensures consistent performance in harsh conditions |
Cleaning and Descaling |
Removes contaminants from the stainless steel surface |
Prevents buildup of harmful substances, maintains passive film effectiveness, extends service life |
A well-formed passive film prevents rust and other forms of degradation. Passivation also improves the longevity and durability of stainless steel products.Industries rely on passivation to maintain the integrity of stainless steel components.
- Passivation increases the lifespan of stainless steel by preventing corrosion.
- The process ensures consistent performance in harsh conditions.
- Passivation is essential for maintaining the quality of stainless-steel alloys.
Regular upkeep ensures that stainless steel maintains its structural integrity.
Regular Maintenance Benefits:
- Prevents buildup of harmful substances on the metal surface
- Maintains the effectiveness of the passive film
- Extends the service life of stainless-steel components
Techniques for Effective Cleaning
Effective cleaning techniques are vital for maintaining stainless steel's corrosion resistance, which help remove dirt and debris without damaging the passive film.
Non-abrasive methods preserve the integrity of the metal surface. Techniques such as ultrasonic cleaning and chemical descaling offer efficient ways to maintain stainless steel.
Recommended Cleaning Techniques:
- Use mild detergents or specialized cleaning solutions for stainless steel.
- Avoid abrasive materials that scratch the surface.
- Employ ultrasonic cleaning for thorough removal of contaminants.
Regular cleaning and descaling ensure that stainless steel remains resistant to corrosion.
Proper maintenance practices contribute to the long-term performance of stainless steel alloys.
Common Corrosion Challenges in Stainless Steel
Corrosion Type |
Causes |
Impact |
Prevention Strategies |
Pitting and Crevice Corrosion |
Breakdown of protective layer, stagnant solutions |
Weakening of metal, potential failures |
Regular cleaning, barrier coatings, design considerations |
Stress Corrosion Cracking |
Tensile stress + corrosive environment |
Cracking, degradation |
Heat treatment, protective coatings, material selection, regular monitoring |
Regular monitoring and maintenance ensure early detection of potential issues, allowing for timely intervention.
Practical Tips for Enhancing Corrosion Resistance
Grade |
Composition |
Applications |
300 Series |
High chromium and nickel |
Harsh environments, chemical processing, marine applications |
400 Series |
Lower chromium and nickel |
Less aggressive conditions, automotive exhaust systems, kitchenware |
Understanding the specific application helps in choosing the right stainless alloys.
Considerations for Specific Environments
Environmental factors play a significant role in determining the best stainless steel grade.
Environment |
Suitable Grade |
Marine |
High molybdenum content (e.g., 316 stainless steel) |
Industrial (acidic/alkaline) |
300 series stainless steel |
Evaluating these conditions ensures optimal performance and longevity.
Protective Coatings
Protective coatings enhance the lifespan of stainless steel by providing an additional barrier to environmental attacks.
Various protective coatings exist, each tailored to specific needs.
- Epoxy Coatings offer robust protection against chemical exposure.
- Ceramic Coatings resist high temperatures and wear.
Selecting the right coating depends on the intended use and environmental challenges.
Application Methods and Benefits
Several methods are used to apply protective coatings, each offering unique advantages.
- Spray Application allows even coverage and quick drying.
- Dip Coating ensures thorough protection for complex shapes.
Proper application maximizes the benefits of coatings, reducing the corrosion rate significantly.
Coatings extend the service life of stainless steel parts by up to 60 percent, making them a cost-effective solution for enhancing corrosion resistance.
In Sum
The chromium shield plays a crucial role in corrosion resistance, forming a protective oxide layer preventing rustiand enhancing the durability of stainless steel. Key strategies for enhancing corrosion resistance include maintaining the integrity of this layer through proper material selection and regular maintenance.
Optimizing chromium content and exploring innovative alloys are the future of corrosion-resistant materials. Understanding these principles ensures the longevity and performance of stainless steel in various environments.