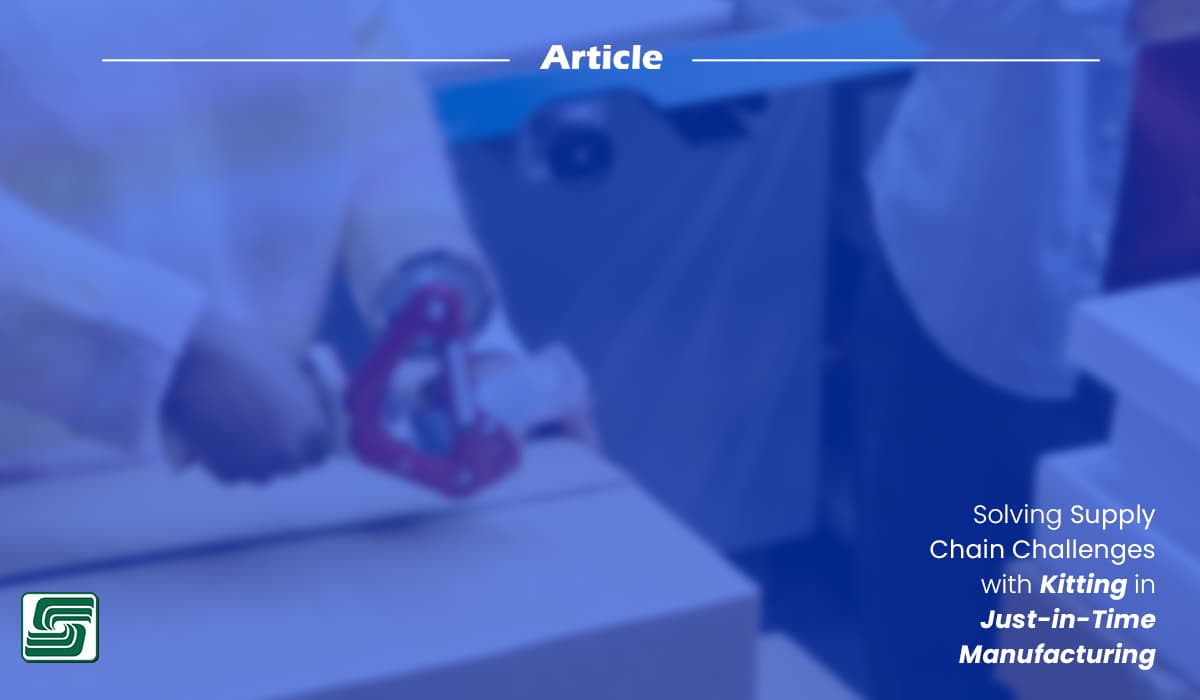
Kitting involves gathering and packaging all the components and parts for a particular assembly or production process. This meticulous preparation ensures that all required items are conveniently accessible at the point of use, minimizing downtime and enhancing overall productivity.
The Connection Between Kitting and Just-in-Time Manufacturing
In Just-in-Time Manufacturing, kitting serves as a strategic enabler. Manufacturers operate with leaner inventories and reduce storage costs by having components readily available exactly when needed.
This synchronization between supply and production aligns seamlessly with the principles of just-in-time methodologies, fostering a more agile and responsive manufacturing environment.
The Importance of Kitting in Modern Manufacturing
The significance of kitting in modern manufacturing cannot be overstated. It streamlines production processes and contributes to waste reduction, improved workflow efficiency, and enhanced quality control.
Embracing kitting empowers manufacturers to optimize their operations while maintaining a competitive edge in today’s dynamic market landscape.
The Role of Kitting in Streamlining POU Activities
In manufacturing, POU (Point of Use) activities are critical in ensuring operational efficiency and minimizing waste.
Understanding the significance of kitting in streamlining POU activities is essential for manufacturers seeking to optimize their production processes.
What Does POU Mean in Manufacturing?
In manufacturing, POU refers to the strategic placement and organization of necessary components, tools, and materials at the precise location where they are used.
This approach eliminates unnecessary movement within the production environment, reducing lead times and enhancing workflow efficiency.
Why POU Matters in Just-in-Time Production
POU is pivotal in aligning to minimize waste and maximize value in just-in-time production.
By ensuring that required items are available precisely where needed, manufacturers significantly reduce excess inventory, lower carrying costs, and enhance responsiveness to customer demands.
Kitting as a Solution for POU Efficiency
An exemplary instance of kitting optimizing POU activities is observed in automotive assembly plants.
Here, essential components such as nuts, bolts, and fasteners are meticulously organized into kits corresponding to specific assembly stages.
This practice ensures that assembly line workers have immediate access to the parts without searching or retrieving them from distant storage locations.
Benefits of POU Kitting
Implementing kitting at the point of use yields multifaceted benefits. It reduces time spent searching for components and minimizes errors by ensuring that the correct parts are readily available.
This approach enhances workplace safety by minimizing clutter and congestion around workstations while promoting a more organized and efficient production environment.
How Pre-Assembly Kitting Enhances Just-in-Time Production Model
Pre-assembly kitting is a strategic practice that involves meticulously gathering and packaging components and parts required for specific production stages before they are needed.
This proactive approach aligns seamlessly with the principles of the Just-in-Time Production Model, contributing to enhanced operational efficiency and waste reduction.
Its Role in Just-in-Time Manufacturing
In just-in-time manufacturing, pre-assembly kitting catalyzes seamless production processes. Manufacturers significantly reduce setup times, minimize disruptions, and optimize overall workflow efficiency by preparing and organizing essential components in advance.
This approach supports lean manufacturing principles and fosters a more agile and responsive production environment.
The Impact of Pre-Assembly Kitting on Production
Pre-assembly kitting reduces downtime by ensuring all necessary components are readily available at each production stage. This proactive preparation:
- Minimizes Interruptions
- Streamlines Assembly Processes
- Saves Substantial Time.
Manufacturers effectively minimize excess inventory and overproduction waste by precisely packaging required parts in advance.
What is Bulk Kitting?
In bulk kitting, the precise gathering and packaging of several components and parts are necessary for multiple assemblies or production processes.
Unlike traditional kitting, which focuses on individual assembly units, bulk kitting encompasses the preparation of components in larger quantities, often tailored to meet the demands of extended production runs or diverse product lines.
How Bulk Kitting Differs from Other Kitting Methods
The primary distinction lies in the scale and scope of preparation.
While conventional kitting focuses on assembling components for specific products or assemblies, bulk kitting extends this practice to encompass a broader range of components, simultaneously catering to multiple production requirements.
This approach enables manufacturers to proactively address varying demand scenarios while maintaining operational agility.
The Benefits of Implementing Bulk Kitting
Bulk kitting yields substantial cost savings by streamlining inventory management and reducing setup times.
Manufacturers leverage economies of scale, negotiate favorable procurement terms, and minimize carrying costs associated with excessive inventories by preparing larger quantities of components in advance.
This proactive approach contributes to significant efficiency improvements by ensuring that essential components are readily available for extended production runs, minimizing downtime, and optimizing overall workflow efficiency.
The Advantages of Bulk Kitting in Manufacturing
In modern manufacturing, bulk kitting represents a strategic approach to optimizing production processes and enhancing operational efficiency.
Manufacturers who want to streamline their operations must grasp the complexities of bulk kitting and its unique benefits.
Comparing Kitting Methods
Here is a comparison table for the different kitting methods:
Feature |
Bulk Kitting |
Conventional Kitting |
Pre-Assembly Kitting |
Point-of-Use Kitting |
Description |
Components are gathered in large quantities and stored as a bulk inventory. Items are then picked and packed as needed for production. |
Components are gathered and packaged in individual kits before the start of production. |
Components are pre-assembled into sub-assemblies or modules before being packaged into kits. |
Kits are created at the point of use, close to the production line, as and when required. |
Lead Time |
Longer lead time as components need to be picked and packed for each production order. |
Moderate lead time as kits are pre-assembled. |
Shorter lead time as sub-assemblies are pre-assembled. |
Shortest lead time as kits are created on-demand. |
Inventory |
Higher inventory levels as components are stored in bulk. |
Moderate inventory levels as kits are pre-assembled. |
Lower inventory levels as sub-assemblies are pre-assembled. |
Lowest inventory levels as kits are created just in time. |
Space Utilization |
More space is required for the bulk storage of components. |
Moderate space utilization as kits are pre-assembled. |
Less space is required as sub-assemblies are pre-assembled. |
Smallest space utilization as kits are created on-demand. |
Flexibility |
It is less flexible as components must be picked and packed for each production order. |
Moderately flexible as kits can be customized. |
It is more flexible as sub-assemblies can be easily modified. |
Highly flexible as kits can be created based on specific production needs. |
Quality Control |
Potential for higher quality issues as components are handled multiple times. |
Moderate quality control as kits are pre-assembled. |
Improved quality control as sub-assemblies are pre-assembled. |
Highest quality control as kits are created at the point of use. |
Labor Efficiency |
Less labor-efficient as components need to be picked and packed for each production order. |
Moderately labor-efficient as kits are pre-assembled. |
More labor-efficient as sub-assemblies are pre-assembled. |
Highest labor efficiency as kits are created on-demand. |
In Sum
When kitting is incorporated into just-in-time manufacturing, it brings several benefits that positively impact all aspects of production.
Manufacturers make substantial strides in enhancing workflow efficiency, reducing waste, and increasing productivity by carefully preparing and packaging essential components.
By aligning kitting and just-in-time methodologies, manufacturers create a lean and agile environment that effectively meets the evolving demands of the market.
As modern manufacturing continues to evolve in response to shifting consumer preferences and global market dynamics, it becomes increasingly imperative for manufacturers to embrace innovative practices that drive operational excellence.