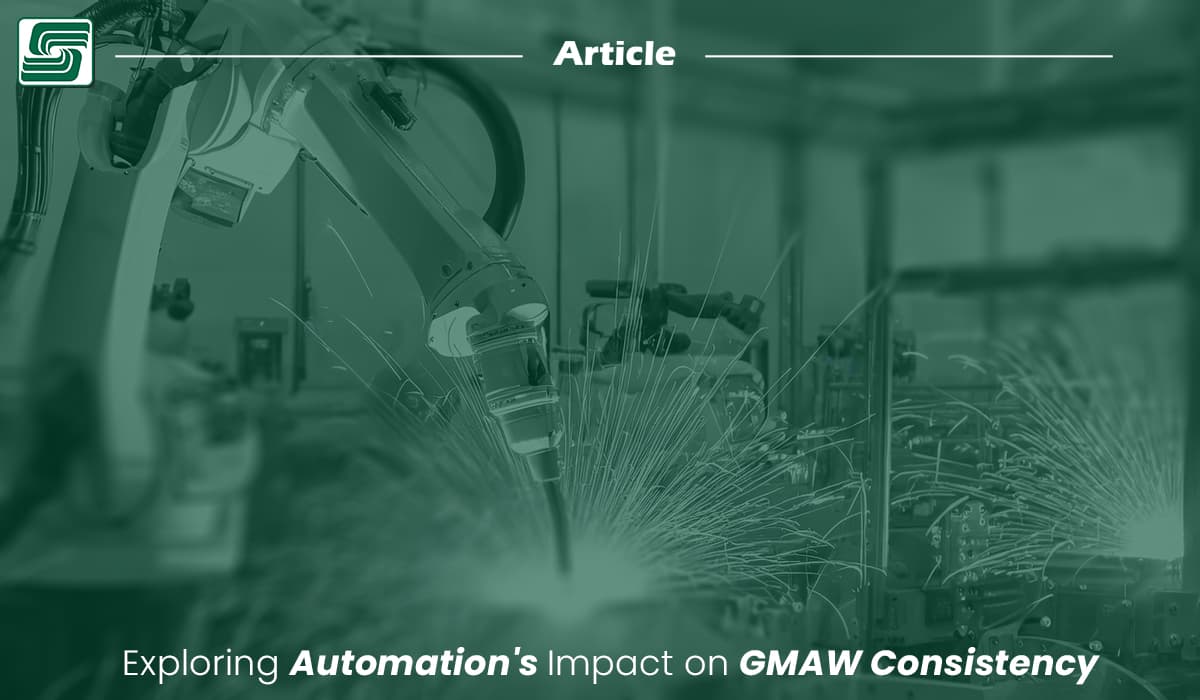
Automating welding transforms the Gas Metal Arc Welding (GMAW) landscape by enhancing precision and productivity. The shift towards automating your arc welding processes addresses critical industry challenges. Labor shortages and quality control issues become manageable with automation. Automating welding ensures consistent weld quality, reduces labor costs, and improves workplace safety. The benefits extend to increased productivity and material efficiency. Automating your arc welding becomes essential for maintaining a competitive advantage as industries evolve. The trend towards automating welding continues to accelerate, promising a future of superior quality and operational efficiency.
Current Challenges in the Welding Industry
Labor Shortages
The welding industry faces a significant challenge with labor shortages. Many companies struggle to find qualified workers. A recent survey highlighted that 47% of respondents identified a lack of skilled labor as the top issue. This shortage stems from an aging workforce, with 41% nearing retirement age. As experienced welders retire, fewer young workers enter the field. This gap creates a pressing need for solutions to attract and train new talent.
Quality Inconsistencies
Quality inconsistencies present another major hurdle. Human welders often produce variable results because of fatigue or lack of experience. These inconsistencies lead to defects in welded products, affecting overall quality. Manufacturers require consistent weld quality to meet industry standards and customer expectations. Variability in welds impacts product reliability and increases costs because of rework and waste.
Efficiency Issues
Efficiency issues further complicate the welding landscape. Manual welding processes often result in slower production rates. Companies face pressure to increase output without compromising quality. Inefficient welding practices lead to longer cycle times and reduced productivity. As industries demand faster turnaround times, efficient welding solutions become more critical. Addressing these efficiency challenges is essential for maintaining competitiveness in the market.
Advantages of Automation in GMAW
Improved Consistency
Automation in GMAW significantly enhances weld consistency. Automated systems maintain precise control over welding parameters, ensuring uniformity across all welds. This precision reduces the variability often seen in manual welding, where human factors like fatigue or inexperience lead to inconsistencies. By eliminating these variables, automated GMAW systems produce high-quality welds that meet stringent industry standards. This consistency is crucial for industries such as automotive manufacturing, where reliable welds are essential for safety and performance.
Enhanced Efficiency
Automated GMAW systems operate continuously, boosting productivity by working around the clock without breaks. This capability allows manufacturers to meet tight production deadlines and scale operations efficiently. Automated welders' speed surpasses manual welders, increasing throughput and reducing cycle times. This efficiency is vital for industries facing high demand and competitive pressures. Automated GMAW systems help companies maintain a competitive edge by minimizing downtime and maximizing output.
Cost-Effectiveness
The cost-effectiveness of automation in GMAW stems from several factors. Automated systems reduce labor costs by minimizing the need for skilled welders and addressing labor shortages in the industry. These systems decrease production time by reducing rework and scrap, leading to significant cost savings. Performing complex welds without root support further enhances cost efficiency, especially in closed-shell structure applications. By optimizing resource use and minimizing waste, automated GMAW systems offer a financially viable solution for modern manufacturing challenges.
Technologies Driving Automation in GMAW
Robotics in Welding
Robotics are pivotal in automating welding processes, particularly Gas Metal Arc Welding. ARC Mate Series robots exemplify the integration of advanced robotics in welding. These robots execute welding tasks with remarkable precision and speed, enhancing productivity and reducing human error. Industries increasingly rely on arc welding robots to streamline operations and maintain consistent weld quality. The versatility of these robots allows them to handle various materials, from aluminum to stainless steel, making them indispensable in modern manufacturing.
Automating welding involves deploying welding cobots that support complex welding tasks. These cobots work alongside human operators, ensuring safety and efficiency. By automating repetitive tasks, they free up skilled workers to focus on more intricate aspects of production. This collaboration between humans and robots optimizes workflow and boosts overall productivity.
Advanced Control Systems
Advanced control systems form the backbone of automated GMAW processes. These systems precisely manage welding parameters, ensuring optimal heat control and minimal spatter. Such enhancements improve short-circuit transfer, making it suitable for thin materials. The ability to fine-tune these parameters allows manufacturers to achieve superior weld quality, even in challenging applications.
Some automated GMAW control systems also facilitate seamless integration with arc welding robots, enabling them to adapt to varying joint conditions. This adaptability proves crucial in industries where precision and consistency are paramount. By leveraging these advanced systems, manufacturers enhance their capability to produce high-quality welds efficiently.
Real-Time Monitoring Tools
Real-time monitoring tools revolutionize how industries approach quality assurance in welding. These tools provide continuous feedback on welding processes, allowing operators to make immediate adjustments. Some automated GMAW control systems integrate real-time monitoring into their arc welding applications, ensuring that every weld meets stringent standards. This proactive approach minimizes defects and reduces the need for rework.
Automating welding with automated control systems involves using these monitoring tools to maintain consistent weld quality. Operators ensure optimal conditions throughout welding by tracking temperature and arc stability parameters. This level of oversight enhances reliability and boosts confidence in the final product.
Impact on Labor and Workforce
Addressing Labor Shortages
Industries face a pressing challenge with labor shortages, particularly in the welding sector. As experienced welders retire, fewer young workers enter the field, creating a gap that automation seeks to fill. Some automated GMAW control systems address this by integrating welding robots into manufacturing processes. These robots traditionally perform tasks by humans, reducing the dependency on skilled labor. Automation offers companies a solution that compensates for the lack of workers and enhances productivity. By automating welding processes, companies maintain their competitive edge despite labor shortages.
Skill Development and Training
The rise of automation in welding causes a shift in workforce skills. FANUC America has created training programs to equip workers with the knowledge to operate and maintain welding robots. These programs focus on developing skills in robotics and automation, ensuring that employees remain valuable assets in an evolving industry. The American Welding Society supports these initiatives by providing certifications that validate expertise in automated welding systems. As workers achieve proficiency in using robots, they contribute to more efficient and reliable production processes.
Job Transformation
Automation transforms jobs rather than eliminates them. Welding with cobots exemplifies this shift, where cobots work alongside human operators. This collaboration allows workers to focus on complex tasks while cobots handle repetitive ones. Some automated GMAW control systems for robotic solutions enhance job roles by introducing new programming and system maintenance responsibilities. As a result, the workforce evolves, adapting to technological advancements and contributing to a more dynamic manufacturing environment.
Quality Control and Assurance
Automated Inspection Systems
Automated inspection systems revolutionize quality control in arc welding. These systems use advanced technologies to ensure precise and consistent weld quality. By integrating collaborative robots into the inspection process, manufacturers achieve unparalleled accuracy. These robots perform detailed inspections, identifying defects that might escape human detection. Using automated systems reduces the need for manual checks, streamlining the quality assurance process. This approach enhances efficiency and minimizes the risk of human error, ensuring that each weld meets stringent industry standards.
Consistent Weld Quality
Consistency in weld quality remains a critical factor in manufacturing success. Automated arc welding systems deliver uniform results by maintaining precise control over welding parameters. This consistency stems from the ability of robots to execute repetitive tasks with exact precision. Unlike manual welding, where fatigue and variability affect outcomes, automated systems always guarantee the same high-quality weld. This reliability is crucial for industries such as automotive and aerospace, where safety and performance depend on consistent weld integrity.
Reducing Human Error
Human error poses a significant challenge in traditional welding processes. Automation addresses this issue by minimizing the reliance on human intervention. Collaborative robots work alongside human operators, handling repetitive and complex tasks precisely. This collaboration reduces the likelihood of errors caused by fatigue or inexperience. By automating critical aspects of the welding process, manufacturers enhance overall quality and reduce the need for costly rework. Integrating advanced control systems further supports this effort, ensuring optimal welding conditions and reducing potential mistakes.
Future Trends in GMAW Automation
Integration with AI and Machine Learning
Integrating Artificial Intelligence (AI) and Machine Learning (ML) into GMAW represents a significant leap forward in automation. AI algorithms analyze vast amounts of data from welding processes to optimize parameters and predict potential issues. This predictive capability enhances the consistency and quality of welds. Machine Learning models learn from past welding operations, allowing them to adapt and improve. By incorporating AI and ML, manufacturers achieve higher precision and efficiency in arc welding, reducing the likelihood of defects and rework.
Expansion of IoT in Welding
The Internet of Things (IoT) transforms the welding industry by connecting machines, sensors, and systems. IoT-enabled devices in arc welding provide real-time data on performance, temperature, and other critical parameters. This connectivity allows for remote monitoring and control, ensuring optimal conditions throughout welding. Manufacturers benefit from increased transparency and the ability to make data-driven decisions. The expansion of IoT in welding leads to improved productivity and reduced downtime, as issues are identified and addressed promptly.
Sustainable Welding Practices
Sustainability is becoming a priority in the welding industry. Automated GMAW systems contribute to this goal by minimizing waste and energy consumption. Advanced control systems ensure precise material usage, reducing excess and scrap. Automated arc welding processes operate with greater efficiency, lowering energy requirements. Manufacturers reduce their environmental impact by adopting sustainable practices and enhancing their reputation and competitiveness. The focus on sustainability aligns with global efforts to create a more eco-friendly industrial landscape.
Automation in Gas Metal Arc Welding has transformed the welding industry by enhancing consistency and productivity. Integrating advanced technologies, such as robotics and real-time monitoring tools, ensures precise control over welding processes. This precision leads to high-quality welds, reducing human error and increasing efficiency. GMAW's versatility and ease of use make it ideal for high-volume production in industries like automotive and manufacturing. As automation continues to evolve, the future of welding promises even greater advancements, offering improved speed, control, and sustainability in welding practices.