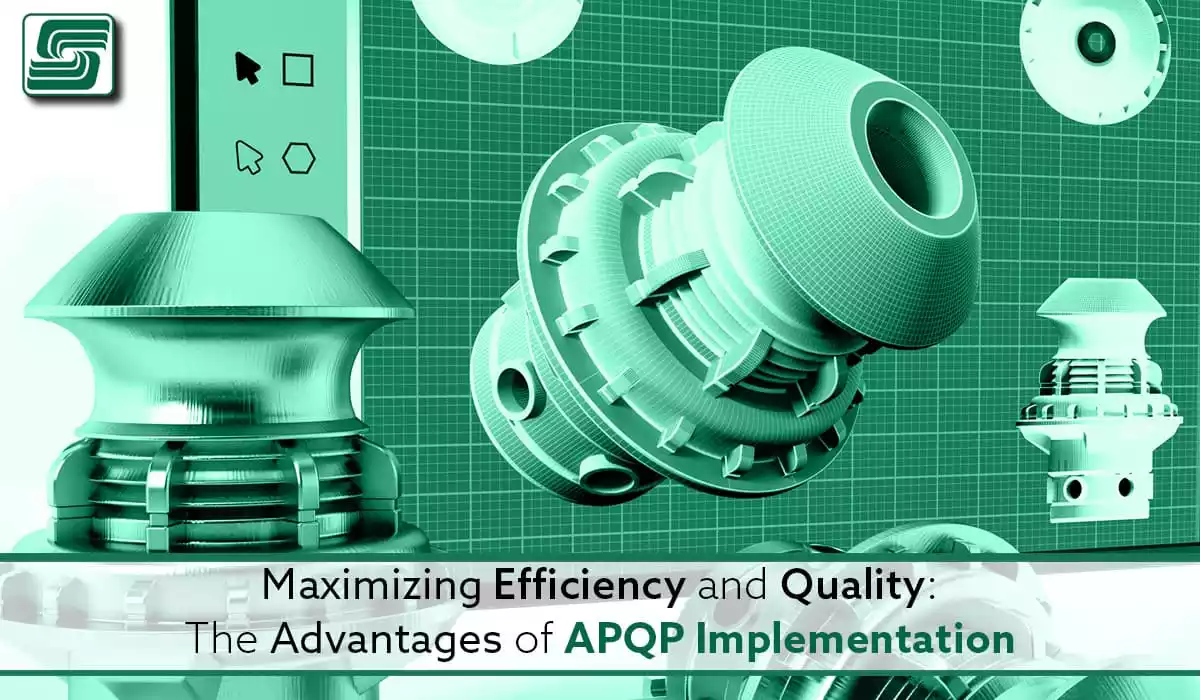
“If you don’t know where you are going, you’ll end up someplace else.” – Yogi Berra
If you're a fan of any sport, you know that a great deal of effort goes into creating a game plan.
For example, let's consider a college football game. Teams use any means at their disposal to scout opponents, learning tendencies and weaknesses; while simultaneously designing offensive and defensive schemes taking advantage of what they've learned.
Successful teams plan successfully. Businesses too.
In today's competitive marketplace, businesses must efficiently produce high-quality products and services. Advanced Product Quality Planning (APQP) is a structured approach to product and process design that can help companies achieve this.
APQP methodologies minimize errors, reduce costs, and improve customer satisfaction by carefully planning and executing each step of the product development process. This article explores the advantages of APQP implementation and how it benefits an organization.
What is APQP?
APQP is a structured approach to product and process design, helping companies minimize errors, reduce costs, and improve customer satisfaction. APQP methodologies use risk management, process flow analysis, and performance metrics to ensure each step of the product development process is carefully planned and executed.
APQP is a framework that guides organizations in developing new products and improving existing products.
APQP Key Components
The key components of APQP include:
- Defining customer requirements.
- Establishing design and process feasibility.
- Conducting risk assessment.
- Developing a detailed product and process plan.
- Performing product validation.
- Implementing production controls
Defining Customer Requirements
Defining customer requirements is a crucial step in APQP. It involves identifying and understanding the needs and expectations of the customers for the product or service developed, which includes gathering and analyzing customer feedback, conducting market research, and engaging in direct communication with customers.
Clear and specific customer requirements serve as the foundation for the subsequent stages of APQP and guide the entire product development process.
Establishing Design and Process Feasibility
Once the customer requirements are defined, the next step determines the feasibility of the product design and the associated manufacturing processes, which involves evaluating whether the design can meet the specified requirements and if the production processes can consistently produce the desired product.
Feasibility studies may include computer-aided design (CAD), computer-aided engineering (CAE), and simulation tools to assess various design and process parameters, such as manufacturability, cost, performance, and reliability.
Conducting Risk Assessment
Risk assessment is a critical component of APQP that involves identifying and analyzing potential risks that could affect the quality, delivery, or overall product's success, including assessing risks associated with design complexity, technology, supply chain, regulatory compliance, market demand, and other factors.
Risk assessment tools, such as Failure Mode and Effects Analysis (FMEA), systematically identify and prioritize potential risks to proactively mitigate or eliminate risks through the appropriate risk management strategies and contingency plans.
Developing a Detailed Product and Process Plan
Developing a detailed product and process plan is a key aspect of APQP, which creates a comprehensive roadmap that outlines the necessary steps and activities to transform the product concept into a final, marketable product.
The product plan includes elements such as design specifications, a bill of materials (BOM), prototype development, testing requirements, and validation criteria.
The process plan details the manufacturing processes, production volumes, resource requirements, and timelines, guiding the entire product development team and helping thoroughly address all aspects of the product and its production.
Performing Product Validation
Product validation is a crucial stage in APQP that involves testing and verifying the product design and performance against the defined requirements by conducting various tests, experiments, and simulations to ensure the product meets the desired quality, functionality, and performance standards.
Validation activities may include functional testing, durability testing, environmental testing, safety testing, and compliance testing with applicable regulations and standards. Product validation results inform any necessary design or process adjustments before moving forward.
Implementing Production Controls
Implementing production controls is the final step in APQP, focused on ensuring consistent and reliable product production by establishing and implementing quality control measures, process controls, and inspection procedures to monitor and verify the manufacturing processes are operating within specified parameters and producing products that meet the defined quality standards.
Production controls may include process audits, Statistical Process Control (SPC), visual inspection, quality checkpoints, and supplier management to ensure the quality and integrity of the final product.
By following these key components of APQP, organizations can enhance their product development processes, minimize risks, and improve overall quality and customer satisfaction.
How does APQP differ from traditional quality planning?
Traditional quality planning focuses on inspecting finished products to identify defects and improve quality. APQP, on the other hand, is a proactive approach that emphasizes the prevention of defects through careful planning and control of the product development process.
APQP methodologies focus on identifying potential risks and opportunities early in the product development process, which allows for the development of more effective solutions and reduces the likelihood of defects.
What phase of APQP is a PPAP?
A Production Part Approval Process (PPAP) is a key component of the product and process validation phase of APQP.
PPAP is a process that verifies that the final product and process designs meet established quality standards by including document submission, the validation of product and process designs, and the establishment of control plans.
In Sum
APQP is a structured approach to product and process design, helping organizations minimize errors, reduce costs, and improve customer satisfaction.
APQP methodologies use risk management, process flow analysis, and performance metrics to ensure that each step of the product development process is carefully planned and executed—a proactive approach that emphasizes the prevention of defects through careful planning and control of the product development process.
Whether a small startup, a large corporation, or even a college football program, APQP helps maximize efficiency and quality and ultimately achieve greater success in today's competitive marketplace.