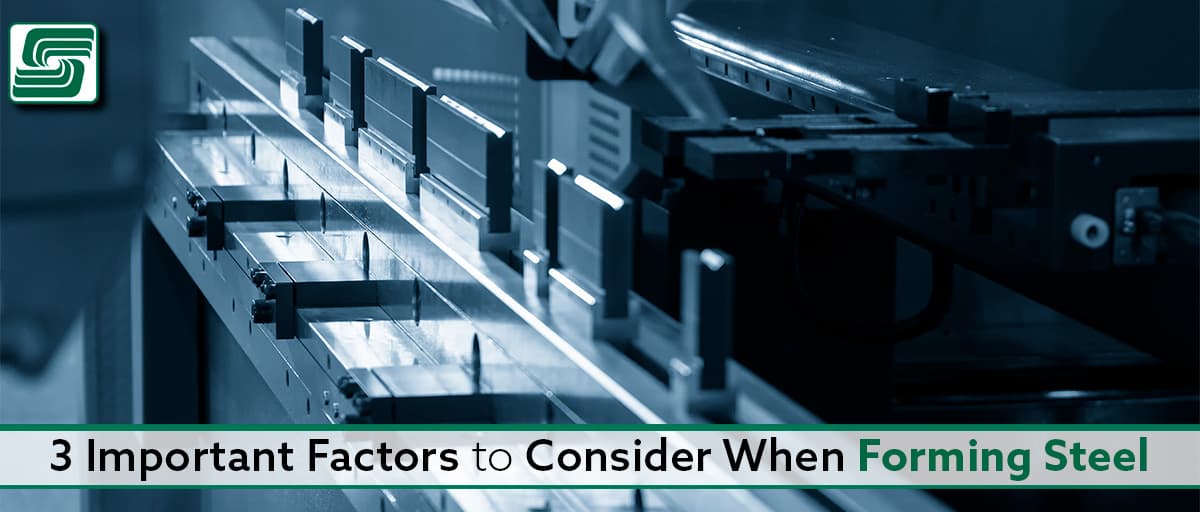
In human history, iron has always been underfoot. Several thousand years passed until tribesmen noticed something stuck to stones and minerals, iron (iron ore). Because of superstition and religious beliefs, early miners used rituals to placate their higher powers while separating the iron components.
Once the ancient world learned a more natural way of separating iron ore, the Bronze Age ended, and the Iron Age began nearly 4,000 years ago.
As time passed, technology and science refined the process of forming and punching steel. Today, metal fabricators learned to look for three important factors when forming steel.
Fabrication Techniques
The metal fabrication industry uses many materials, techniques, and tools, to create reliable products.
As you would expect, these products have various applications and should be high-performing. Popular fabrication techniques include:
Punching
(1) Shearing holes in sheet metal with a punch and die. (2) The die shearing of a closed contour in which the sheared-out sheet metal part is scrap. (3) Forming metal components using a punch.
Welding
Welding is a process for joining similar metals. Welding joins metals by melting and fusing the base metals joined and the filler metal applied. Welding employs pinpointed localized heat input.
Most welding involves ferrous-based metals such as steel and stainless steel. Welding covers a temperature range of 1500 °F - 3000 °F.
Weld joints are usually stronger than or as strong as the base metals being joined. Typically, welding is used for forging, blacksmithing, oil pipelines, and food equipment applications.
Stamping
A term refers to various press-forming operations in coining, embossing, blanking, and pressing. Forming metals using pressure into the surface of a metal, usually a strip or sheet.
Blanking
The operation of punching, cutting, or shearing a piece out of stock to a predetermined shape. Die-cutting of the outside shape of a part.
Drawing
A term used for various forming operations, such as deep drawing a sheet metal blank, redrawing a tubular part, and drawing rod, wire, and tube.
The usual drawing process about sheet metal working in a press is a method for producing a cup-like form from a sheet metal disk by holding it firmly between blank holding surfaces to prevent the formation of wrinkles. In contrast, the punch travel produces the required shape.
In steel forming, the stretch rig or compressing of a sheet metal part into a die by a punch creates a 3-dimensional part. The process of cold forming a flat pre-cut metal blank into a hollow vessel without excessive wrinkling, thinning, or fracturing.
Bending
A term typically applied to a metal-forming process. it is the creation of a formed feature by the angular displacement of a sheet metal workpiece. the straining of material, usually flat sheet or strip metal, by moving it around a straight axis lying in the neutral plane.
Metal flow occurs within the plastic range of the metal so that the bent part retains a permanent set after removing the applied stress. the cross-section of the bend inward from the neutral plane is in compression; the rest of the bend is in tension.
Cutting
To separate any portion of a workpiece from any other part of the same workpiece by a step of machining (e.g., grinding, drilling, boring, milling, planing), severing (e.g., breaking, sawing, slicing, shearing), or by the intrusion of a sharp-edged or pointed tool without removal of material (e.g., stabbing, splitting, intrusive punching).
Roll Forming
A continuous bending operation in the metal forming process, in which sheet or strip metal is plastically deformed along a linear axis, passing through a series of roller dies and progressively shaping to the desired contour.
3 Factors of Forming Steel
The method of choice depends on the intended application and its distinctive specifications and unique requirements. Just as crucial as choosing the correct fabrication technique is, so is material selection. It speaks more to cost control and, most importantly, the integrity of the final design. Steel, aluminum, stainless steel, and various other alloys are some of the common materials in the industry.
These materials are readily available. For an industry using expensive tools and machinery, these metals are cost-effective. Before punching and forming steel, a company must ensure that they use the most suitable material depending on the final product's intended purpose. How do they do this? They consider the following three factors:
Hardness
A material's hardness measures how much it withstands or resists localized plastic deformation as a direct result of either mechanical indentation or abrasion. It also indicates surface indentation, scratching, penetration, or shaping resistance.
Several testing methods determine the hardness of steel, including
These methods provide numerical results. The higher the hardness number, the harder the steel. Unlike popular belief, steel hardness has nothing to do with the alloy's stiffness. Parts of the same sheet of steel may differ, but its stiffness always remains constant.
Thickness
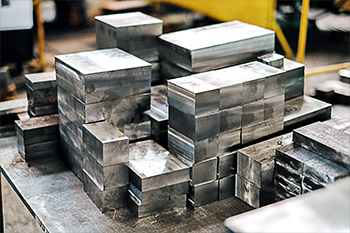
When referring to sheet metal, use the term "gauge.". Gauges, or rather the gauge system, specify the thickness in a sheet of metal using either millimeters or inches as its units of measurement.
Like hardness scales, many gauge systems exist. The higher the gauge number, the thinner the sheet of steel is; the same applies to other metals. 16-gauge steel is thicker than its 18-gauge counterpart.
Depending on the fabrication project, a company decides whether to use high- or low-grade steel. Thickness plays a crucial role when measuring the hardness of steel, especially using the Rockwell scales. If the sheet is thin, you must use a load that won't force the indenter to penetrate through the metal.
Grain Direction
Steel, like most other metals, is a poly-crystalline material. The metal is made of millions and millions of minute crystals, otherwise known as grains.
Making up these crystals are tiny cubes, invisible to the microscope but noticeable as collective cubical units. They arrange themselves within the material, forming planes that are parallel to the cubes' axes. Some of them may align diametrically and form cleavage planes, which are areas of weakness.
As mentioned earlier, metal and steel fabrication involves several techniques. These techniques impact the crystalline structure's alignment within the material. The final result is subject to the overall percentage of grains aligning with their preferred orientation. This orientation highlights the importance of the line grain direction.
If crystals are not in their desired orientation, you see mill scale, defects, blemishes, and scratches on the final product. Engineers must follow the principle of grain direction – line grain should run perpendicularly to bend.
In Sum
I don't know if you've ever had to split hardwood. When splitting dried oak or elm, you consider the same three factors when forming steel. You need to know what direction the grain moves, how hard, and the thickness of that block of wood.
I struggled until my dad showed me how to 'read' the wood. Even after he taught me the right way of splitting wood, it was still hard work, yet if I ignored his advice, it would've been exponentially harder.
Skillfully reading steel ensures the best possible outcome when forming steel. A skill honed by excellent instruction and experience.